Different Types of Blenders
LKMixer have Different Types of Blenders for sale. The mixer is a mechanical equipment that uses mechanical force and gravity to evenly mix two or more kinds of materials. In the process of mixing, the contact surface area of the material can also be increased to promote chemical reactions; It can also accelerate physical change.
Commonly used mixers are divided into four categories: gas and low viscosity liquid mixers, medium and high viscosity liquid and paste mixers, powder and granular solid material mixing machinery.
Commonly used mixers are divided into four categories: gas and low viscosity liquid mixers, medium and high viscosity liquid and paste mixing machinery, thermoplastic material mixers, powder and granular solid material mixing machinery.
Gas and low-viscosity liquid mixers are characterized by simple structure, no rotating parts, small maintenance and repair, and low energy consumption. This kind of mixing machinery is divided into four kinds: air mixing, pipeline mixing, jet mixing and forced circulation mixing.
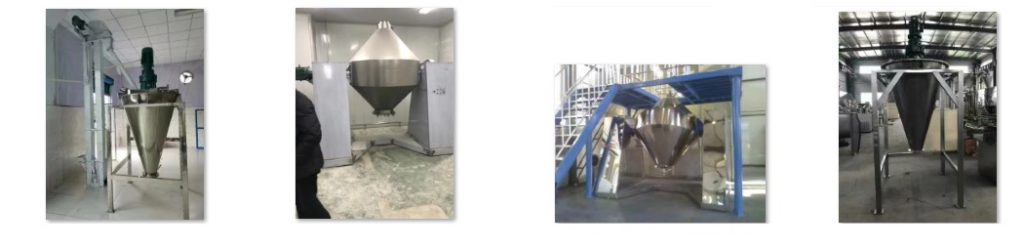
Mixer accessories are mainly made of wear-resistant alloy materials, including high-speed stirring scraper, stirring wing, wear-resistant liner, stirring arm, stirring shovel, planetary shovel, stirring plow knife, stirring rod, stirring rake and so on
The mixing machinery of medium and high viscosity liquids and pastes generally has a strong shearing effect.
Thermoplastic material mixing machinery is mainly used for mixing thermoplastic materials (such as rubber and plastic) with additives; Powder, granular solid material mixing machinery is mostly intermittent operation, but also includes both mixing and grinding machinery, such as wheel rolling machine.
The moving parts of the mechanical agitator also have shear effects on the liquid when rotating, and the liquid is also subjected to shear effects when flowing through the wall of the device and various fixed components installed in the container, which will cause many local vortex diffusion.
For liquids with different density and composition, which are not mutually soluble, the shear action and strong turbulence produced by stirring will tear the dense liquid into small droplets and disperse them evenly into the main liquid.
Types of Blenders
Common mixers are: plow knife mixer, screw belt mixer, no gravity mixer, V-type mixer, double spiral cone mixer, high and low speed liquid mixer, planetary power mixer and so on.
Double helix conical mixer
Cone mixer is a new type of high efficiency and high precision particle mixing equipment, it is widely used in chemical industry, pesticides, dyes, medicine, food, feed, petroleum, metallurgical mining and other industries of various powder particles mixing.
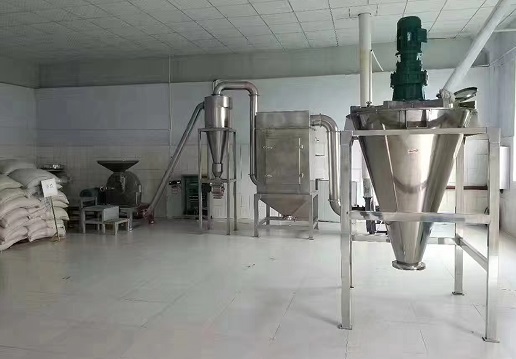
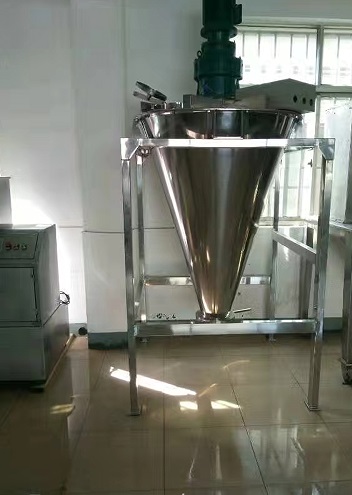
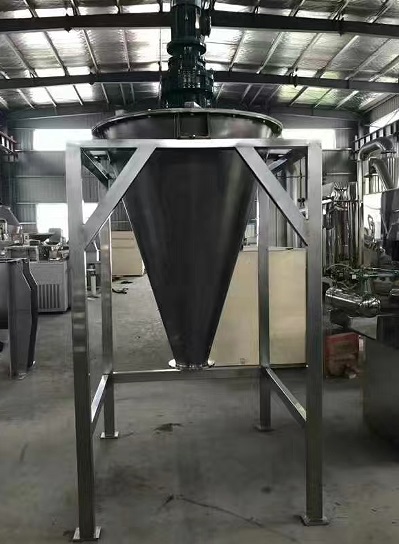
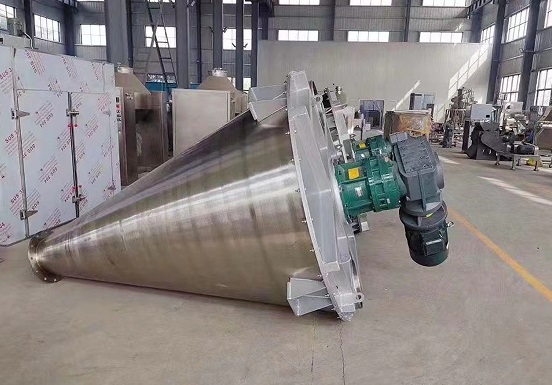
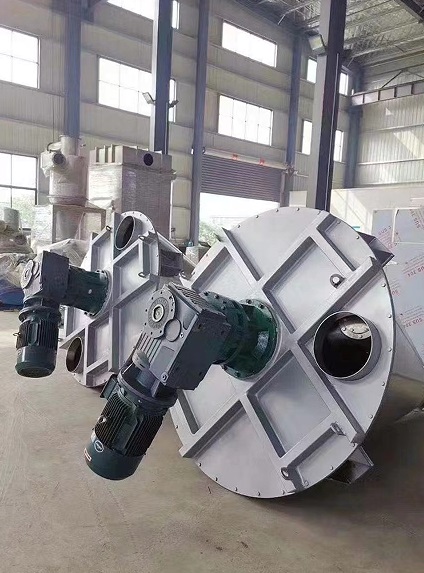
Two, the main characteristics
- (1) Advanced structure, easy operation, safe and reliable operation.
- (2) The mixing speed is fast and the quality is uniform. The double helix of the machine is asymmetrically arranged, which enlarges the mixing range of one big and one small, so it is more suitable for the mixing of materials with different proportion.
- (3) The energy saving effect is remarkable, and the energy consumption of the machine is only one-tenth of that of the drum mixer.
- (4) The wear and pressure feed of granular materials are small, and there is no overheating reaction to the mixing of heat-sensitive materials.
- (5) The mixed preparation is stable and does not occur stratification and segregation.
- (6) The machine is sealed dust-free, simple operation, easy maintenance, long service life. In addition, the cone can also be made into a pressure vessel for pressure or vacuum operation according to user requirements.
- (7) The autobiography and revolution of the machine are completed by a set of motor and cycloidal pin transmission reducer.
Third, the working principle
- (1) Due to the rotation of the double helix, the powder particles operate around the cone wall.
- (2) Due to the autobiography of the spiral blade, the powder is discharged to the center of the cone for radial movement.
- (3) The powder flows upward from the bottom of the cone and is discharged to the surrounding surface outside the spiral for material mixing.
- (4) The downward flow of powder particles caused by spiral rotation is precisely due to the combination of spiral rotation in the mixer, forming four flow forms of powder: that is, the composite movement of convection, shear, diffusion and infiltration. Therefore, the powder can be quickly mixed evenly in the mixer.
Double helix conical mixer for sale
Horizontal ribbon mixer
Horizontal double-axis screw belt mixer is used to mix dry and powdery materials for the purpose of mixing evenly. When mixing, the material inside is moved by two rotors moving in opposite directions to carry out a compound movement. The two-axis blade drives the material along the inner wall of the groove to rotate clockwise and backward; the material near the axis center rotates axially from inside to both sides; the external spiral drives the material near the cylinder wall to rotate axially from both sides to inside. As a result, the convective circulation in the material cylinder and shear infiltration mixing are caused, and the material is quickly and evenly mixed in a short time.
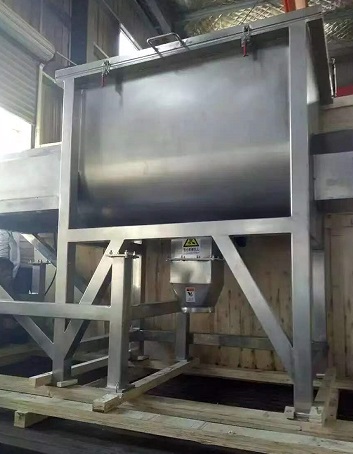
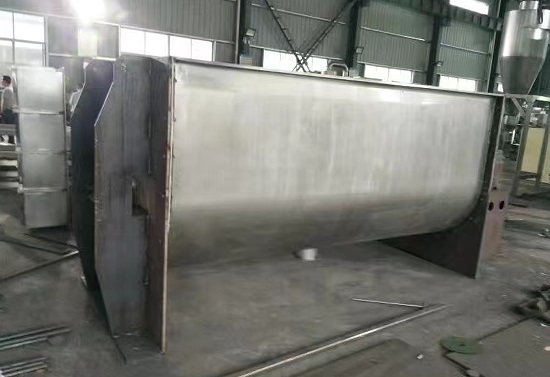
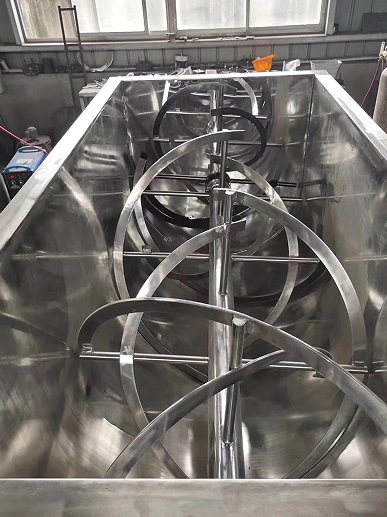
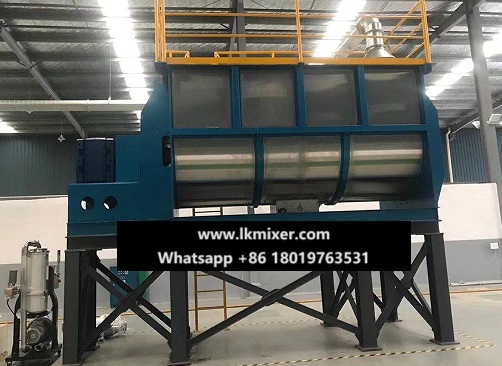
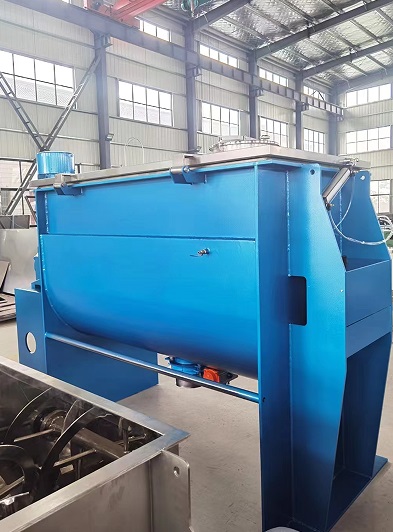
Product features:
- U-shaped barrel structure, smooth operation, uniform mixing, no dead Angle, clean discharge, wide application range.
- The use of internal and external double-layer screw belt staggered mixing, mixing speed is fast, high uniformity
- The bearing is at both ends of the mixer, the material is not easy to enter, and the maintenance rate is low.
- The screw conveyor is easy to feed, the feed port is flush with the ground, and the feed is labor-saving and convenient.
- The internal structure and the overall design materials have passed ISO9001 international quality system certification.
Horizontal two-axis screw belt mixer working principle:
The machine consists of two parts: feeding and mixing. - Feeding part: Enter by the hopper, lift the material into the mixer through the spiral blade into the mixing cylinder for mixing.
- Mixing part: When the material enters the mixing cylinder for round-trip staggered movement, the mixing effect is good.
Horizontal ribbon mixer for Sale
Three dimensional swing mixer
The principle of the oscillating mixer is different from that of the traditional rotary mixer. It TURBULA the material in the mixing cylinder by turbula, Turbula, Turbula, Turbula, Turbula, Turbula, Turbula and Turbula. An alternate pulse is generated to continuously push the material, and the turbulence generated by the movement has a changing energy gradient, so that each particle in the mixed material has an immovable state, and each particle constantly changes its position in the frequent movement and diffusion, resulting in a satisfactory mixing effect.
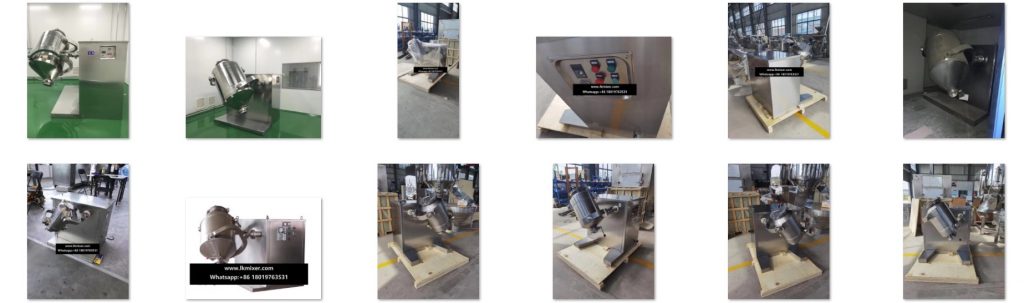
The three-dimensional swing mixer is composed of frame, drive system, three-dimensional motion mechanism, mixing cylinder and electrical control system, etc. The mixing cylinder in direct contact with the material is made of high-quality stainless steel material, and the inner wall of the cylinder is precisely polished.
Series 3D swing is a novel material mixer widely used in pharmaceutical, chemical, food, light industry and scientific research institutions. The machine can mix powder or granular materials with good flow performance very evenly, so that the mixed materials can achieve the best effect.
First, performance characteristics
1, with multi-direction movement, so that the material mixing points in the cylinder body, the mixing effect is significant, the mixing uniformity is higher than the uniformity of the general mixer;
2, three-dimensional swing mixer mixing cylinder design body inner wall after precision polishing.
Second, equipment installation
- The machine is unloaded, loaded and tested before leaving the factory. Normal work before factory, to meet the user’s safe use;
2, transport mode: 600 litre (including 600 type) using the whole factory, do not prepare footing, bolts; 600-litre above the use of split transport, preparation of footing, bolts.
Iii. Operation
1, the machine adopts electromagnetic speed regulation (or frequency converter speed regulation), before starting, turn on the total power, the power indicator light, then start the motor button, and then start the on-off switch on the speed regulation panel (the frequency converter can press the touch button), the indicator light, and then slowly rotate to reach the normal mixed speed;
2, if the user needs temple mixing time, it should be formulated in the contract, our factory may install time relay, the user according to the mixing requirements of the material to specify the mixing time;
3, after the end of mixing, turn off the machine according to the boot order, if you find that the feeding is not ideal, you can click the button to meet the feeding requirements.
Precautions
1, the mixing of the machine is three-dimensional space mixing, adding safety protection bars in the effective range of the material bobbin, so as to avoid life safety accidents. Before starting, do not stand in front of the cylinder to avoid accidents;
2, when loading and unloading, the electric power of the equipment must be stopped to prevent the electrical failure, causing unnecessary accidents.
Vacuum drying mixer
How it works:
The double-cone vacuum drying mixer is a double-cone rotary tank. In the vacuum state, the tank leads to steam or hot water in the jacket for heating, and the heat contacts with the wet material through the inner wall of the tank. The vapor evaporates after the wet material absorbs heat and is pumped away through the vacuum pump through the vacuum exhaust pipe. Because the tank is in a vacuum state, and the rotation in the tank makes the material constantly turn up and down, inside and outside, it speeds up the drying speed of the material, improves the drying efficiency, and achieves the purpose of uniform drying.
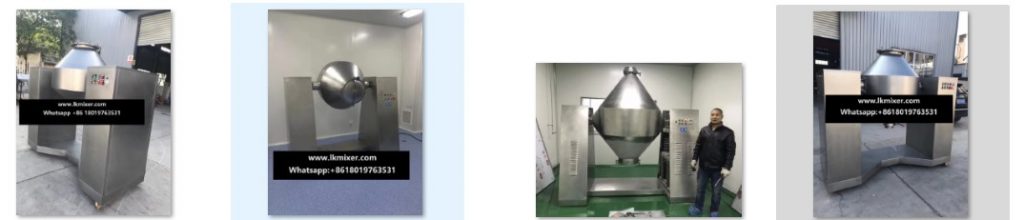
Purpose:
This machine is used for vacuum drying and mixing of powder and granular materials in pharmaceutical, food, chemical and other industries, especially for materials with the following requirements:
1, can not accept high temperature heat sensitive materials;
2, easy to oxidize, dangerous materials;Materials that need to recover solvents and toxic gases;
- Materials requiring very low residual volatile matter content;
- Materials with requirements for crystal shape;
Vacuum Drying Mixer for Sale
How to Choose the Right Model:
Many users in the powder, powder mixing equipment many choose the original domestic vertical cone mixing equipment, but experts suggest that because the vertical cone mixer has many shortcomings, the maintenance rate is high, so in the powder/powder or granular material mixing, should choose the horizontal mixer, the equipment mixing efficiency is high, mixing quality is good, unloading time is short, the residual amount is also small. However, the selection and use of horizontal mixer should pay attention to the following points:
1, according to the daily production of the selection of bed mixing machine. Because each batch of material processing time of the mixer is about 10 minutes, plus the time of discharging and feeding, each batch of material processing time can be measured by 15 minutes, then 4 batches of material can be processed continuously in 1 hour. If you choose a mixer with a processing capacity of 100 kg per batch, you can process 400 kg per hour. Users can choose horizontal mixers according to their needs.
2, according to the working principle of the horizontal spiral belt mixer, the ability of the double spiral belt used for mixing to push the material in the opposite direction should be basically consistent. Because the pitch of the inner spiral belt should be smaller than the outer spiral belt, in order to achieve the ability to push the material is consistent, the pitch of the inner spiral belt should be smaller than the outer spiral belt, and the width should be greater than the outer spiral belt, otherwise the material will be concentrated in one direction. Therefore, pay attention to this when choosing a horizontal mixer.
3, according to the design principle, the gap between the spiral belt and the shell in the spiral belt mixer can be 4 mm ~ 10 mm, and the material can be driven by friction to all participate in the mixing. However, because the grinding particle size and the friction coefficient of the material are not the same, the time of mixing of various components of the material is not the same, resulting in the non-uniformity of the product. Some manufacturers have realized this and have made improvements to their products. One is to pay attention to the machining accuracy, so that the bottom gap is reduced to about 3 mm; The other is to make the position between the spindle and the housing in the form of adjustable, according to the amount of wear can often adjust the gap between the spiral belt and the housing. When choosing a mixer, these two forms of products should be the best choice.
4, choose the horizontal spiral belt mixer should pay attention to the discharge method. Should communicate with the supplier in time to choose the valve form suitable for their own process, and do not choose the discharge form of the side mouth. The reason is: when the mixer completes the mixing in the specified time, the uniformity of the material can be ensured by clearing it once in the shortest time; If the side screw belt is gradually released, one is to delay the time, not to reach the expected productivity, and the other is that the material has reached the best uniformity, but excessive mixing will make the material segregation, destroy the uniformity, thus losing the significance of choosing a horizontal mixer.
5, the use of horizontal mixer should pay attention to the order of feeding. Generally, aniseed is first cast, such as corn meal, soybean meal, etc., and then cast group feed, such as premix. Pay attention to the premix must not be fed by the screw elevator, the application of one-time tipping bucket feeding, or manual feeding, so as to avoid the segregation and loss of the active ingredients in the premix.
- The horizontal mixer should be fed batch by batch after the mixer is started. Do not stop when the mixing is finished, and mix a batch after the net material. If you start again after full load, it will cause the power distance to be too large and burn the motor.
Choosing a suitable horizontal mixer and using it properly will significantly improve the quality of the mixture and will soon reflect a positive effect in the production process. If you can further master the technology of self-mixing, you can also greatly reduce the cost of materials, thereby increasing profits.
You may also interest in:
About LKMixer
LKMixer is a professional manufacturer for fertilizer production line, grinder, mixer and granulator, shredder. These machines are widely used in food, pharmaceutical, cosmetic, health care products and chemical industries. The Food materials like Peanut, mushroom, seeds, potato, bean, tobacco, salt, cannabis, tea, Sugar, corn, Coffee, rice, pepper, grain as so on. Grinders have many types such as Pulse Dust Grinder which suitable for zero pollution environment, Turbine Mill which is suitable for coffee bean, 12-120mesh all can meet, Ultrafine Grinding Mill covers 80-200mesh, and also Winnowing Dust Grinder or other grinding machines like SF Hammer. Welcome to contact us for details. Contact us for more information. Proposal, catalog, quotation. Mobile/WhatsApp: +86 18019763531 Tel: +86 21 66037855 Email: sales@lkmixer.com