BHLSG Wet Granulator
- Material: powder and powder, powder and bond;
- Capacity: 230-320KG;
- Volume: 50-800L;
- Total Power: 5.5-45KW
- Application: Pharmaceuticals, Nutraceuticals, Food Products, Chemicals, Fertilizer, Stucco, Clay, Potting Soils.
- Notice: This is just an examplePlease contact with our sales for choosing the right model.
Wet Granulator Parameter:
Model | Volume(L) | Max Loading(KG) | Cutter Speed(rpm) | Rotating Speed(RPM) | Mixing Power(KW) | Granulation Power(KW) |
BHLSG-50 | 50 | 30 | 50-3000 | 100-400 | 5.1 | 3 |
BHLSG-100 | 100 | 40 | 50-3000 | 80-270 | 11 | 4 |
BHLSG-200 | 200 | 80 | 50-3000 | 80-270 | 15 | 5.5 |
BHLSG–300 | 300 | 120 | 50-3000 | 60-220 | 22 | 7.5 |
BHLSG-400 | 400 | 160 | 50-3000 | 50-220 | 30 | 7.5 |
BHLSG-600 | 600 | 240 | 50-3000 | 40-180 | 37 | 11 |
BHLSG-800 | 800 | 320 | 50-3000 | 30-120 | 45 | 15 |
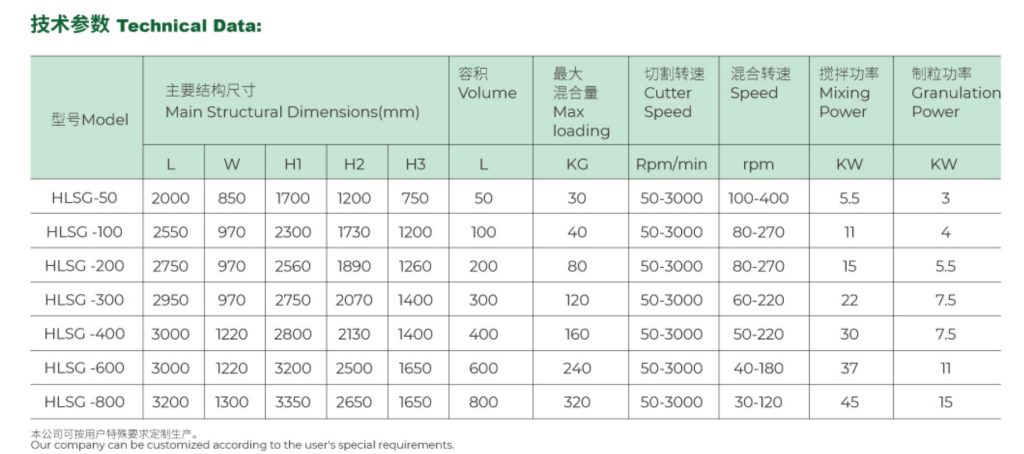
Wet Granulator Price:
The Wet Granulator according to different model is around $580~$12,000. For more price information Please click.
Business Type: | Manufacturer/Factory | Main Products: | Mill, grinder, granulator, mixer, Crushing Equipment |
Number of Employees: | 100 | Year of Establishment: | 2014.05 |
Production Capacity | 5000 Set/Year | After-sales Service: | Technical Support; on-line teach lessons |
R&D Capacity: | ODM, OEM | Annual Output Value: | US$5 Million – US$10 Million |
No. of R&D Staff: | 5 | No. of Production Lines: | 6 |
LK Mixer is a professional manufacturer for grinder, mixer and pulverizer, granulator. These machines are widely used in pharmaceutical, cosmetic, health care products and chemical industries. Our main product including granulating machine, grinder, mixer, dryer, etc. All mechanical products in accordance with the China GMP design requirements. And also we have other certifications such as CE, UL for motors.
Business Philosophy
“Quality is the main policy of sales” and “integrity is the principle of success” are the business philosophy of our people. We carry out one-year warranty, lifelong maintenance service, with technical consultation, with material test machine and other services, and long-term supply of equipment. Welcome new and old customers to negotiate cooperation!
Certifications:
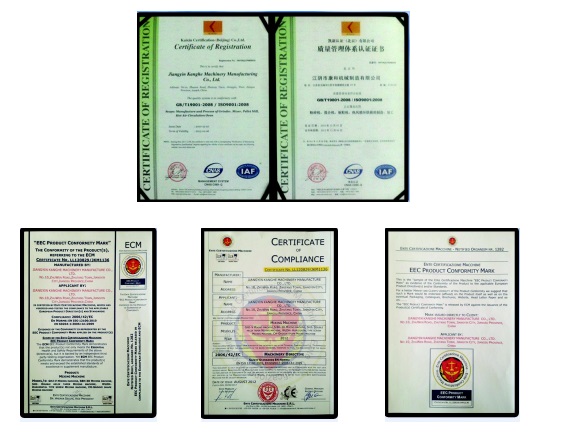
Industrial Pepper Grinder Diagram of Design
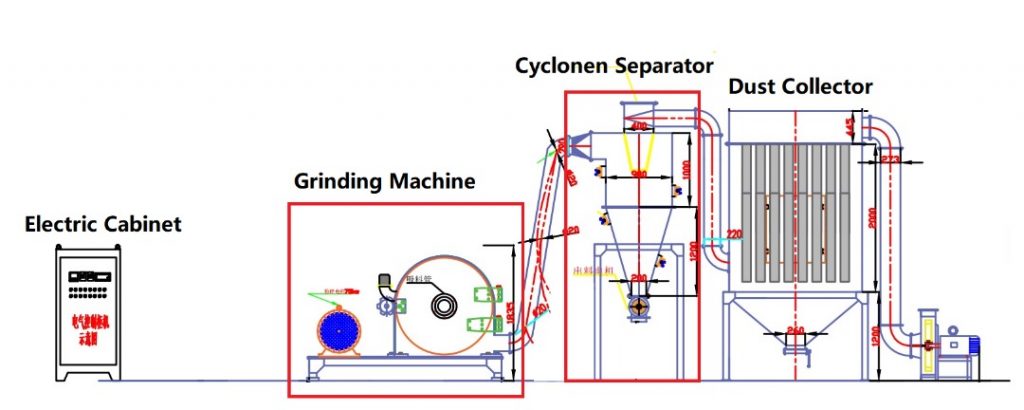
Electric Cabinet with UL Certification
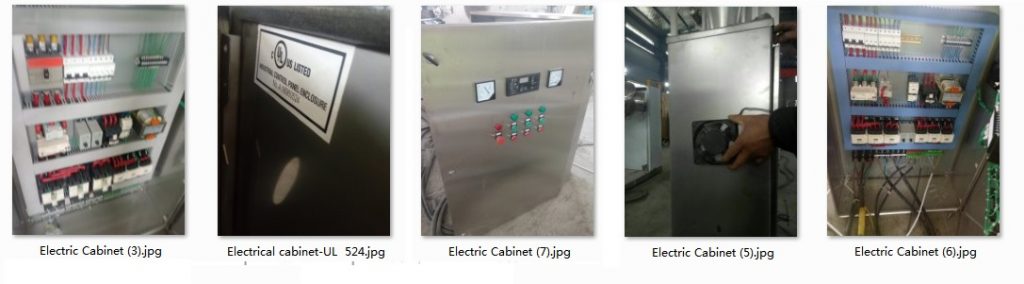
Cyclone Processor and Motors:
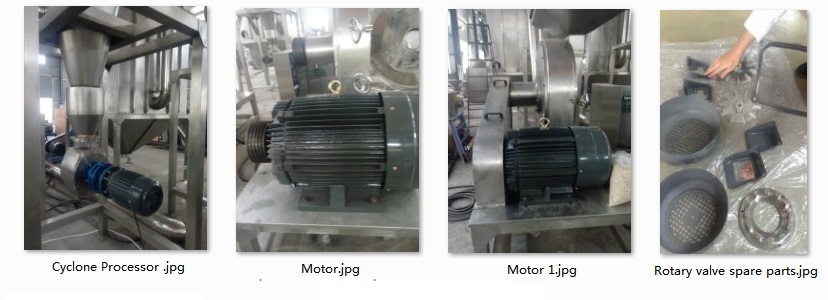
Spare Parts:
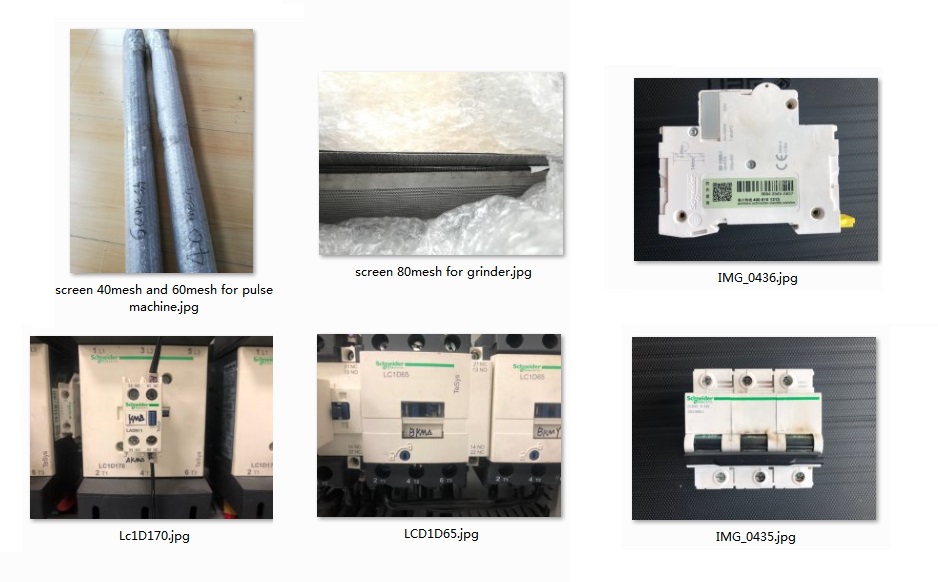
Small Machine Packing:
Small machine packed with export fumigation-free wooden cases, goes with bulk shipment or in container.
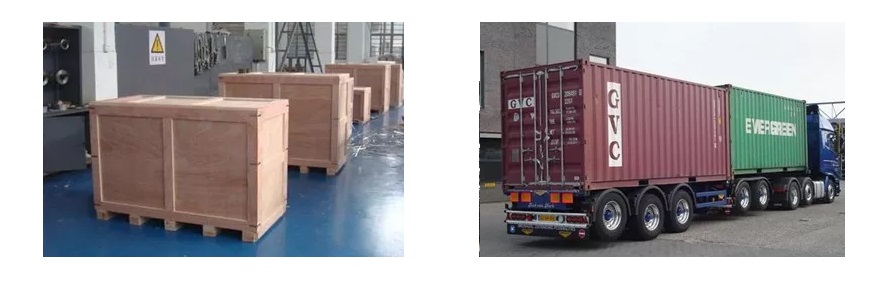
Large Machine Packing:
Shipment Show Case: Small grinder machine ship for Masala, Pakistan, Kenya, Nepal, India…
Wet Granulator for Sale Review :
What is Wet Granulator:
Wet granulator is a kind of equipment that processes powdered materials into granular materials. Wet granulation can solve the shortcomings of small accumulation density of powdered materials, poor fluidity, difficult to accurately measure, easy to fly pollution, so as to reduce transportation costs and material losses, reduce powder pollution and safety risks, and is widely used in the field of carbon black granulation, fly ash granulation, fertilizer granulation.
What is the Process of Wet Granulator:
The process consists of two programs including mixing and granulating:
Powder metrical can be charged into the material pan from the conical hopper and continue to rotate in the container under the action of mixing blade once the hopper is closed. in the meanwhile, all materials grow up the shape of liquid bridge under continuous effects of conical tank wall. Under the action of extrusion, friction as well as crumb by blade and conical tank wall, all material is gradually turn for loosen. At last , while opening the hopper outlet, waterish particles are pushed off under the centrifugal effects of blade.
These soft particles are formed not dependent on forced extrusion effects, more exactly; mainly these small and uniform particles are formed after continuous cutting under the simile-liquid state. in al, this machine can realize the mutual transformation between different materials.
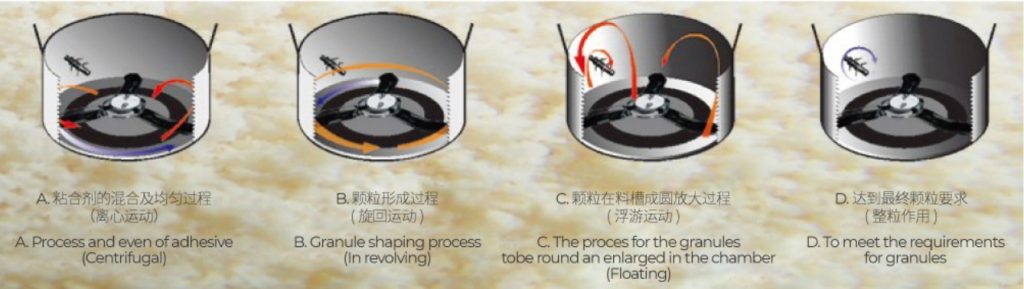
Wet Granulator Feature:
- 3.1 The whole machine is made of SUS304 stainless steel, which meets all kinds of specifications and requirements; Models with 316L material can also be made according to user requirements.
- 3.2 Principle, can save the use of adhesive, and easy to dry.
- 3.3 The granulation time is greatly shortened, and the whole process of mixing and granulation can be completed in a few minutes.
- 3.4 Mixing and cutting can be easily controlled, suitable for different raw materials and different needs of granulation.
- 3.5 PLC man-machine interface control technology commonly used at present, simple and convenient operation, data can be saved, easy to extract parameters.
- 3.6 The operation process is completely closed without any pollution.
- 3.7 Smooth operation and low noise.
- 3.8 Pneumatic sealing drive shaft design, easy to clean; The machine is easy to disassemble and assemble, easy to clear the site without dead corners, in line with GMP requirements.
- 3.9 Granule shape is approximately round, good fluidity, suitable for tablet and capsule filling.
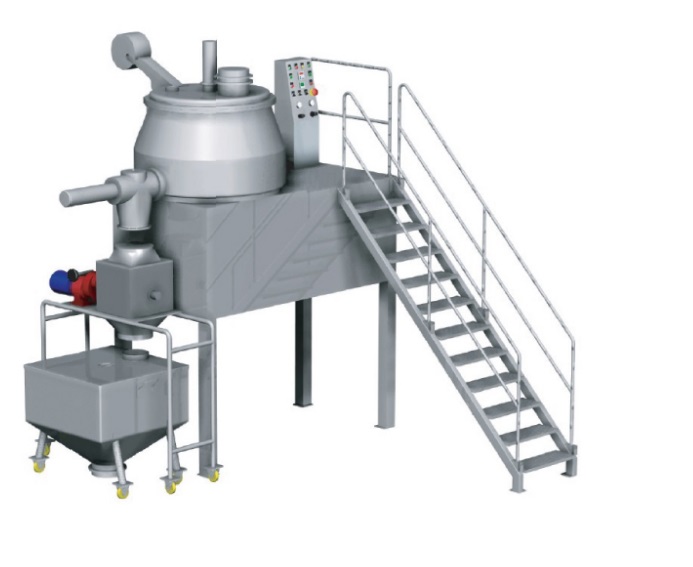
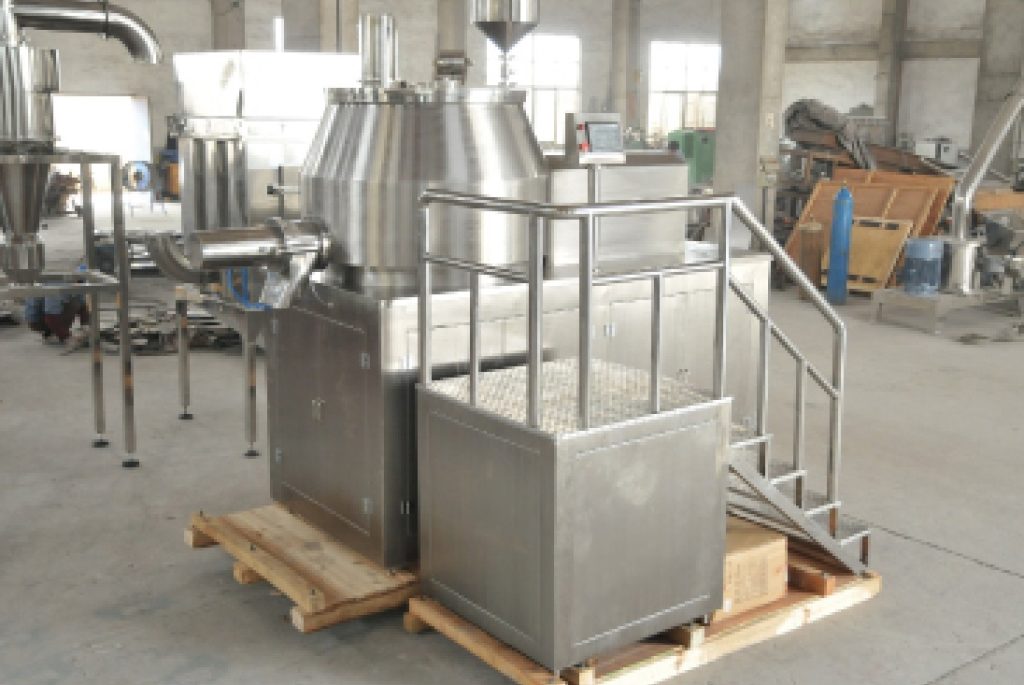
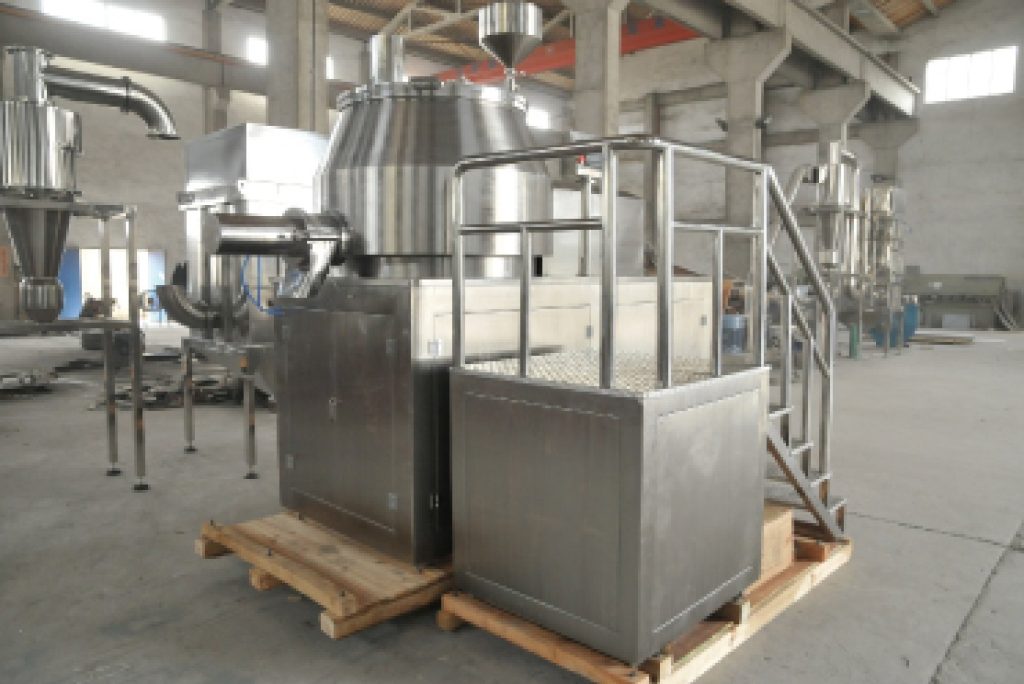
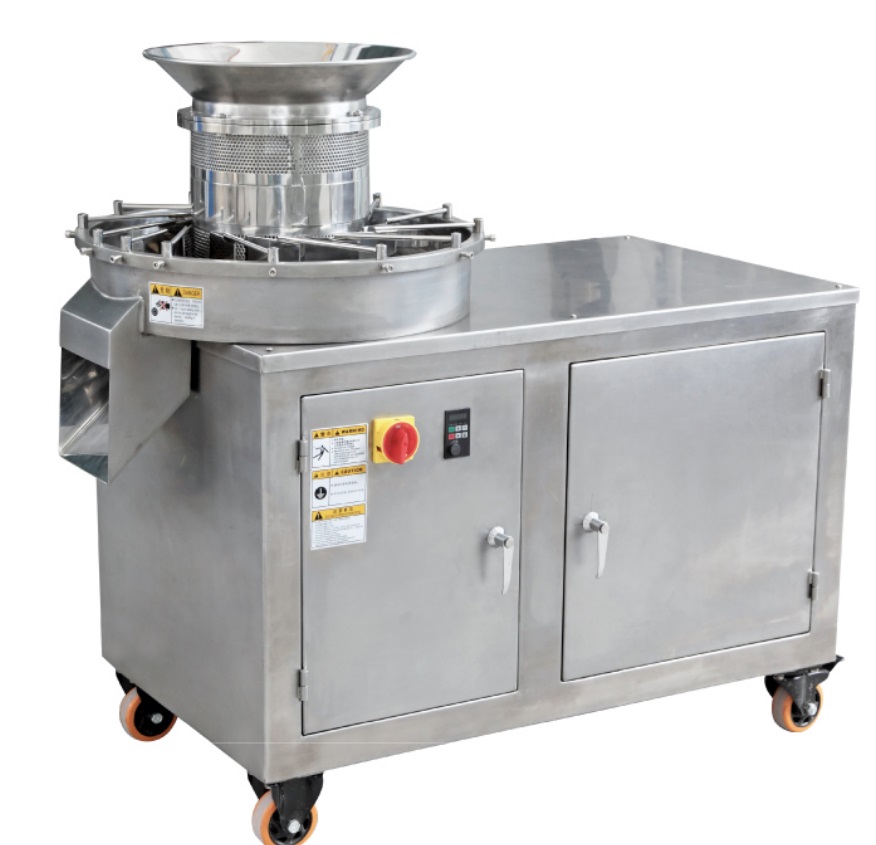
Wet Granulator Function:
Wet granulator is an important granulation equipment, the main role is to powder or granular raw materials by adding water or other wetting agent to make molding particles. The role of the wet granulator is not only to process the raw material into particles, but also to control the size, shape and density of the particles. At the same time, it can also change the adsorption capacity and surface characteristics of the raw material for the adhesive, thereby improving the quality and stability of the finished product.
Wet Granulation Diagram
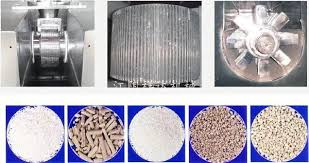
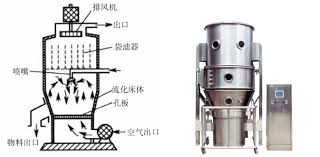
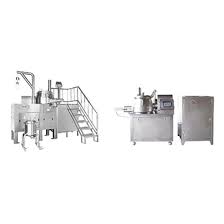
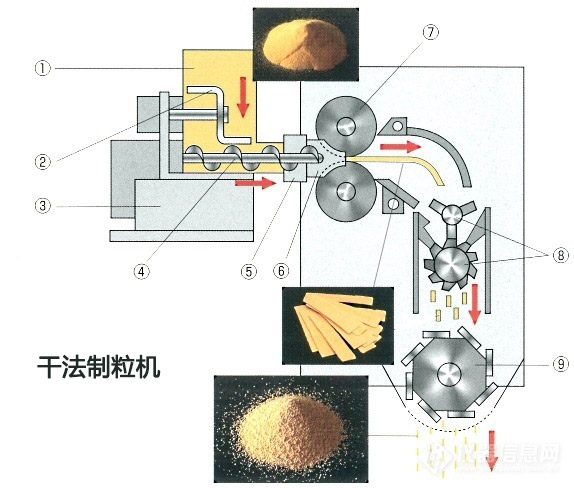
Super Wet Granulator Type:
Single tank
A combination of mixers/granulators, in which the particles can be dried in the same equipment, is often referred to as a single-can processor (or one-can processor). The granulation process is completed in a conventional high shear processor; However, care must be taken to avoid forming clumps during operation, as they cannot disintegrate before drying. There are a few other options for single-pot drying. The basic drying principle depends on the vacuum application in the feeding bowl, which reduces the evaporation temperature of the pelletizing solution. The traditional heat source comes from the inner wall of the heated dryer. The heat transfer depends on the surface area of the inner wall of the dryer and the volume of the product being treated. Therefore, for small-scale organic solvents or a small amount of adhesive liquid, direct heating method is the most effective.
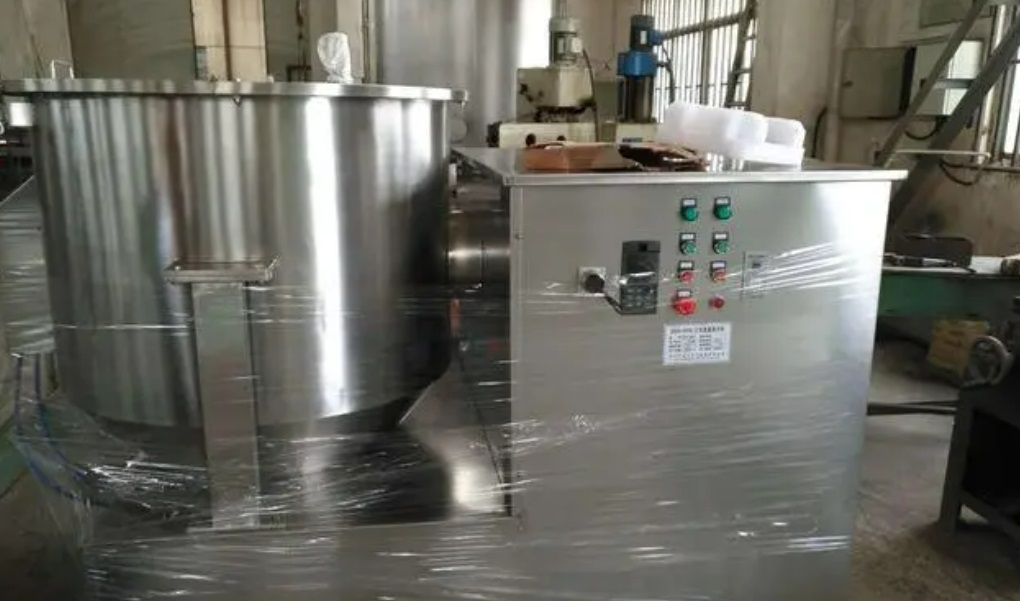
The injection of stripper gas into the tank results in a very low final moisture content (for specific applications only). A small amount of gas is injected into the bottom of the unit and passes through the product fluidized bed to increase the efficiency of transpiration and evaporation. However, since heating the inner wall is the only source of drying energy, linear scaling is not feasible. If the processed material is allergic to heat (which limits the inner wall temperature); If water is used as the pelletizing liquid (its boiling temperature under vacuum is relatively high, and the heat of vaporization is higher than that of organic solvents); This problem is exacerbated if used in mass production (where the surface/volume ratio deteriorates as volume increases).
These limitations can be overcome using microwave power. Microwave energy not only provides an additional energy source, but also has the added advantage that due to the use of organic solvents, only pure organic vapor is treated at the exhaust end, rather than the mixture of solvents and large amounts of process gases required in most other wet.
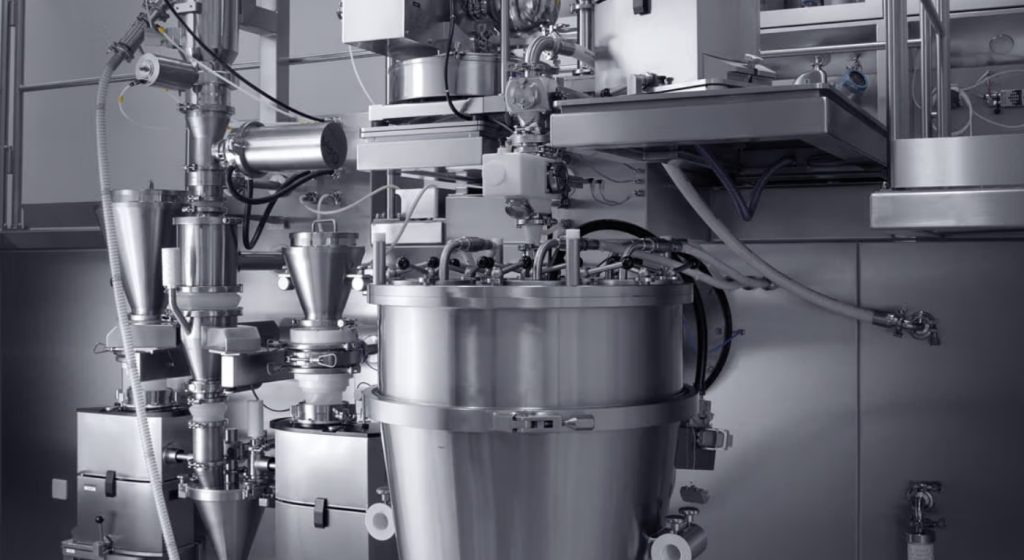
Fluidized-bed spray granulation
A fluidized bed with a spray nozzle can be used for granulation. While the top spray position has been preferred for many years, the advantages of side-spray systems are now clear. The main advantage is the location of the spray nozzle, where the shear force is much higher, so that particle shapes that were previously only possible with high-shear processors can be processed. In addition, the introduction of the new FlexStream™ series fluidized bed can also solve the problem of expanding use. In recent years, in response to the competition of single-tank technology, fluidized bed technology has been advancing by leaps and bounds. Today, as long as it is closely connected to upstream and downstream equipment, it can complete the raw material processing process. In addition, the fully automated in situ cleaning (CIP) of stainless steel filters in fluidized beds has now reached a new level and is superior to single-tank technology.
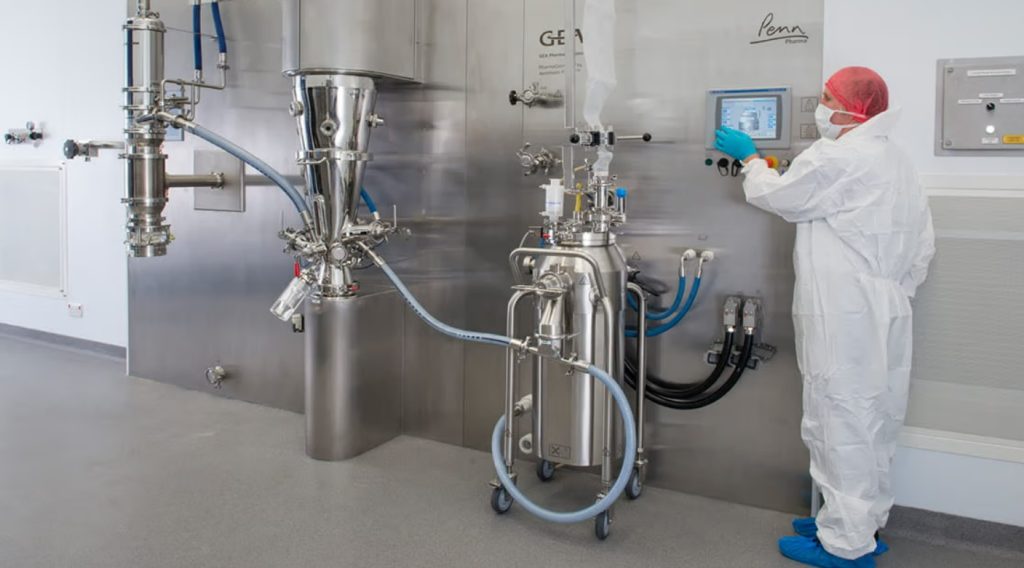
Integrated high shear granulation and fluidized bed drying
This is the most common configuration in industrial-scale drug pelletizing processes. The system can also be fully integrated with upstream and downstream equipment, and can even include a wet mill between the granulator and the dryer. Thanks to a modern control system, it can be easily fed, mixed and granulated in a high-shear granulator, while the previous batch can be dried in a fluidized bed before being sent out. All equipment can be cleaned in situ with one automatic process.
Melt granulation: In the melt granulation process, the adhesive solution of the standard wet granulation process is replaced by a meltable adhesive. This adhesive can be melted and then added, but the high shear process offers the convenience of allowing the addition of a solid adhesive. The friction of the mixer and the heat transferred by the heated shell of the bowl can melt the adhesive.
Effervescent products: Add a small amount of water to start the pre-effervescent reaction: some carbon dioxide is released during the granulation process, but water is also a reaction product; It acts as a granulation fluid, producing more carbon dioxide and more water. At a certain point, a drying process must be initiated to remove water to halt the reaction. This can be done using a high shear pelletizer with a subsequent liquid drying function to feed the raw material at the end of the pelletizing process to a preheated fluidized bed dryer.
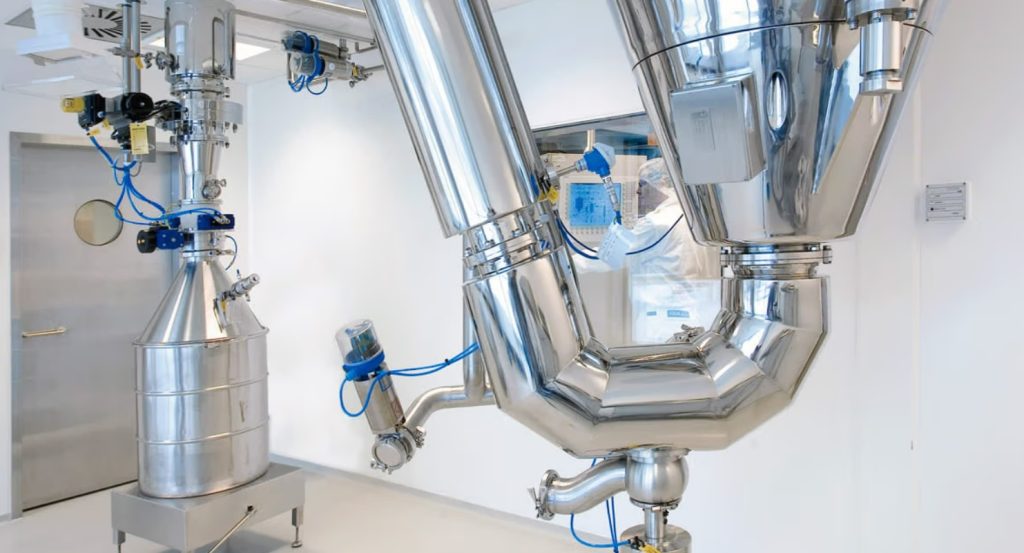
Pharmaceutical Wet Granulators
For drug manufacturers, there are a plethora of granulation technologies on the market. Since granulation technology is very important in the process of oral drug production, this article specifically provides corresponding suggestions for different processes.
Granulation technique
In the pharmaceutical industry, there are three most common granulation processes for the production of solid dosage forms: wet granulation, dry granulation (roll granulation) and direct mixing. The importance of pelletizing in oral drug production (most fine drug compounds need to be treated with pellets to improve their fluidity and processability before being made into tablets), coupled with the wide application of this technology in the pharmaceutical industry, makes it necessary to understand some principles and methods, which I will outline below. The obvious benefit of roller granulation is that it does not produce any water throughout the process, making it an ideal technique for compounds whose physical and chemical states change upon exposure to water. Moreover, it produces particles that do not require drying treatment and are more energy efficient.
Wet Granulation Flow Chart:
- Equipment preparation
- Cleaning: Before using the wet mixing granulator, the equipment must be thoroughly cleaned to ensure that the equipment is clean and pollution-free.
- Check the equipment: check whether the equipment has leakage, loosening, cracking, etc., so as not to affect the granulation effect.
Two, raw material ratio - Ratio calculation: According to the requirements of granulation, calculate the proportion and dosage of the required raw materials.
- Raw material preparation: Prepare the raw materials to be used in accordance with the proportion and place them in the designated position.
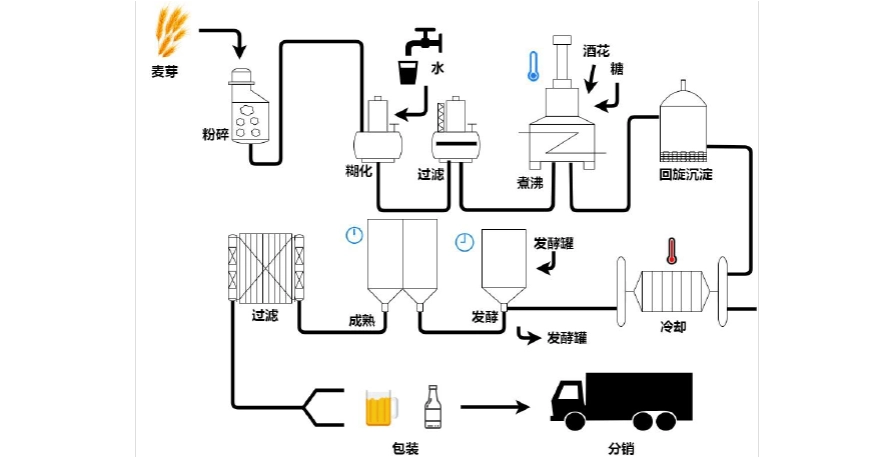
Continuous wet granulation:
Continuous processing systems are in great demand due to a variety of regulatory initiatives to improve product quality and reduce the risk of product defects. The system generally has three modules: wet high shear granulation module, segment dryer module and particle adjustment module. In the granulation module, the dry raw material is injected separately by the system, or the dry raw material is pre-mixed into the continuous high shear granulator. After the small dry mix is complete, the granulation solution is added so that each particle inhales the same amount of liquid. The whole wet granulation process takes only a few seconds and only a few grams of product are processed in a given time, so it starts faster and does not incur any losses. If the particle size needs to be adjusted, the working level of the granulator can be changed; This allows the production of a uniform mass and density of wet particles that flow continuously into the dryer. This process does not produce over-sized condensates, so there is no need for wet grinding.
The dryer module is based on the principle of fluidized-bed drying, which packs a steady flow of particles into 1.5 kg and then sends them to a separate section of the dryer for sub-drying. Once the particles in this section reach the desired moisture level, the dryer sends it to the particle adjustment module, which is then loaded into another package of wet particles ready for processing. The drying curve of each packet is closely monitored. In the particle adjustment module, the system measures the dried particles to conform to key quality parameters such as particle size distribution, humidity and compositional uniformity. The system processes only 6-9 kg of raw material at any one time, thus minimizing the risk of production losses. The system’s small size and modular structure allow for rapid deployment, easy scale-up, and rapid integration with existing equipment.
High shear wet granulation process
In a solid based dispersion in which the fixed powder and liquid coexist, the basic particles of the solid powder are bonded to each other and increased by forced means (such as agent pressure, gravity, centrifugal force, mechanical force, air impulse force, etc.) by using the dispersed self-bonding (or external binder), and a certain shape and uniform particle size are formed.
The complete set of wet process equipment is mainly composed of mixing (kneading), granulation, drying and auxiliary system equipment. After mixing (kneading), the powder enters the granulator to form a wet product with the required particle size, and gets a granular finished product after drying, so as to achieve the purpose of granulation.
Divided into front discharge type and side discharge type, the diameter of the front discharge type granulation product is generally selected between 1.5~12mm, the diameter of the side discharge type granulation product is generally selected between 0.7~2.0mm, the particle shape is cylindrical, and the granulation rate is ≥95%.
The high-speed granulator uses the mechanical mixing force of high-speed rotation and the resulting air power to make the continuous quantitative entry of the fine powder material into the machine and the continuous quantitative injection of the binder (generally water) in the machine fully contact, continuous mixing, granulation, spheroidization, densification and other processes, so as to achieve the purpose of granulation. The pellet shape of the granulation product is spherical, so as to achieve the purpose of granulation. The pellet shape of the granulation product is spherical, so as to achieve the purpose of granulation. The particle shape of the granulation product is spherical, the sphericity is ≥0.7, the particle size is generally between 0.3 and 0.4mm, and the granulation rate is ≥80%.
There is also an extruder granulator with certain mixing, kneading and functions, which can effectively prevent the material from “holding the rod”, especially for the extrusion and granulation production of thixotropic materials. The diameter of the granulated product is generally selected between 1.5 and 12mm, the particle shape is cylindrical, and the granulation rate is ≥95%
Characteristic:
Wet Granulator Applications:
Working Principle:
The picture shows the experimental equipment of high-speed mixing wet granulator. The main materials and auxiliary materials that need to be granulated are added to the mixer according to the appropriate proportion and formula. The powder materials and binders are fully mixed by the bottom mixing paddle at high speed in the cylindrical container to form wet soft materials, and then cut into uniform wet particles by the side high-speed crushing paddle, so as to achieve the purpose of granulation. Vacuum drying and auxiliary system equipment can also be selected to achieve one-step, direct access to finished products.
About LKMixer
LKMixer is a professional manufacturer for fertilizer production line, grinder, mixer and granulator, shredder. These machines are widely used in food, pharmaceutical, cosmetic, health care products and chemical industries. The Food materials like Peanut, mushroom, seeds, potato, bean, tobacco, salt, cannabis, tea, Sugar, corn, Coffee, rice, pepper, grain as so on. Grinders have many types such as Pulse Dust Grinder which suitable for zero pollution environment, Turbine Mill which is suitable for coffee bean, 12-120mesh all can meet, Ultrafine Grinding Mill covers 80-200mesh, and also Winnowing Dust Grinder or other grinding machines like SF Hammer. Welcome to contact us for details. Contact us for more information. Proposal, catalog, quotation. Mobile/WhatsApp: +86 18019763531 Tel: +86 21 66037855 Email: sales@lkmixer.com
Contact Us
FAQ(Click and See More)
Why Choose Us?
We have 20 years manufacturing experiences; 15600 cubic meters factory area; 5000sets annual capacity; 55 professional engineers;
What’s your main maket?
South America: Brazil, Colombia, Peru, Bolivia, Uruguay, Paraguay ;Romania;
USA with UL Certification
Middle East: Saudi, Arabia, Oman, Turkey
Europe: Russia, Australia, Belarus, Ukraine, Poland
Can you support OEM?
– Yes, OEM or ODM. Machine can be customized according to customer detail requirement, including capacity and voltages, motor certifications.
– Drawing and raw materials also can be customized.
What after-sale services?
– 7*24 customer service online;
– 7*24 engineers online services;
– 12 months warranty services.
WHAT kind of MACHINE YOUR COMPANY HAVE?
CAN YOU GIVE ME GUIDE ON OTHER MACHINE ? TO FULL MY PRODUCTION LINE
YES ! Our f have factory build more than 20 years now, we can design and customize whole line, besides of the grinding machine, mixing machine, we can also fully support to provide the washing machine, cutting machine, drying machine, packing machine, filling machine. Though we are not producing these machine, but our brother companies co-work together for over 20 years, we have rich experience in providing you a full effective production line, fully automatically or semi-automatically.
HOW TO VISIT YOUR COMPANY?
Our Factory located in Jiangsu Province, very near to Shanghai, you can fly to Shanghai Pudong Airport, we pick you up and take you by car 2 hours ride, can reach our factory, welcome your visit.
WHAT’S YOUR BEFORE & AFTER SERVICE ?
1) Before your purchasing, we need to know your detail request, such as what kind of material you want to grind and mixing, what final product powder or granule you want to reach. Because different material and powder sizes request of different machine to do. We can provide professional advice and rich experience help to choose machine. Most of the products we have already did before for other customer, trail test or run mass production, so we knows which machine is best in performance of grinding and mixing. This is of very importance in helping you choose the right model. We also wish this can help our customer a lot. Even the material we didn’t do before, we will prepare the same material and to do the trail test and send video to you for your reference.
2) One Year guarantee of machine quality. If the machine have problem within one year, we will send you the spare parts to you for replacement, but this not including the damage caused by human causes. We also have 24 hours on line guide for customer, if you have operation difficulty, we will guide by video and on line communication with our engineer for your emergency debug.
3) For small machine, we sell with whole machine, it’s no need to install, and easy to operation, no problems for operation. While for large machine, its’s also not difficult to install with video guideline, but if you need, we can assign our technicians to go abroad, the round ticket, food and residents will be paid by customer.
HOW ABOUT YOUR PAYMENT TERM?
Our payment term is T/T. 50% payment in advance, rest of 50% payment finish before the goods shipped. When we finish the machine production we will do trail test and run the machine take videos for your green light. You pay the rest of 50% payment then.
What is high speed granulator?
The high speed granulator can be used either as a single unit or in combination with a cooling mixer. The geometric design of the high-speed hybrid tool accelerates the product radially, making it push outward and spiral upward, forming a unique swirl shape.
What is wet granulator?
Wet granulation is a process that uses liquid solutions and adhesives to bind different powder particles together. In the wet pelletizing process, you will need a non-toxic and volatile pelletizing solution to keep the powder particles together.
What is RMG in pharma?
The Rapid mixing granulator (RMG) is used for mixing, stirring and shearing mixing (to break internal molecular forces). It is used in pharmaceuticals to make pellets. The components of the RMG (impeller and chopper) are responsible for the wet granulation process.
What are the different types of granulators?
In terms of processing, pelletizer can be divided into two types: wet pelletizer, which uses liquid in the processing process, and dry pelletizer, which does not use liquid. Wet granulation involves a lot of water and detergent, and the purpose is to clean the contaminated material and also to cool the machine.
Why wet granulation is best?
This is a general purpose process that can be used to produce a variety of particles. It’s a relatively simple process that can be easily scaled up. This is a cost-effective process. It produces particles with good fluidity and uniformity.
Dry Granulator VS Wet Granulator:
Dry granulation: This process allows the production of particles without the use of a solution, as the product that needs to be granulated may be sensitive to moisture and hot air, or have poor compression properties. Water-free granulation requires compacting and crushing the compounds to create uniformly sized, free-flowing particles. Therefore, the initial powder particles need to be aggregated under high pressure using a rocking mixing or high shear mixing granulator. There are two ways of dry granulation: using a heavy tablet press to make a large tablet (pill block), or using two rollers to press the powder to make a tablet (roll press/tablet press). If the tablet press is used for dry granulation, the natural fluidity of the powder may not be good, so it cannot be neatly into the mold cavity, resulting in uneven tablet density. The roller press (pelletizer/compactor) uses a screw feed system, which neatly and evenly feeds the powder between two pressure rollers. The powder is then compressed into strips or pellets by a pressure roller, which is then fed into a low-shear mill for grinding. After the product is properly compressed, it is then passed through the mill for final mixing and finally made into compressed tablets.
Wet granulation: This method of adding a solution to the powder requires the use of a granulation solution to hold the initial dry powder mixture together. The solvent contained in the liquid must be easily volatilized, disappear on its own after drying, and must be non-toxic. Common solutions include water, ethanol, and isopropyl alcohol (single or mixed). The solution can be aqueous (safer) or solvent-based. When the water is mixed with the powder, it forms a strong viscosity between the powder particles, enough to bond them together. However, once the water evaporates, the powder can fall apart. So water may not be enough to stick the particles together consistently and stably. In this case, a solution containing an adhesive is often required. Once the solvent/water has evaporated and the particles have formed a solid lump of powder, granulation is ready.
This process can be extremely simple or complex, depending on the powder and the type of equipment available. In traditional wet granulation, the wet blocks are squeezed into a filter, screened into wet particles, and then dried. This is followed by the sifting stage of the decomposed particle blocks. If water-sensitive drugs are processed or short-time drying of drugs is required, organic solvents should be used as an alternative to drying particles. For many active substances, direct pressing is not the best technique, so wet granulation is still the preferred method. Even though the active substance is sensitive to hydrolysis, modern equipment such as fluidized beds can eliminate all problems in the wet granulation process.
In summary, wet granulation is a granulation method in which a liquid binder is added to the powder mixture. Dry granulation – either continuous direct pressing (CDC) or continuous mixing – is a process in which the active pharmaceutical ingredient (API) and excipient are fed separately and precisely into a continuous mixer.