WF Universal Grinder
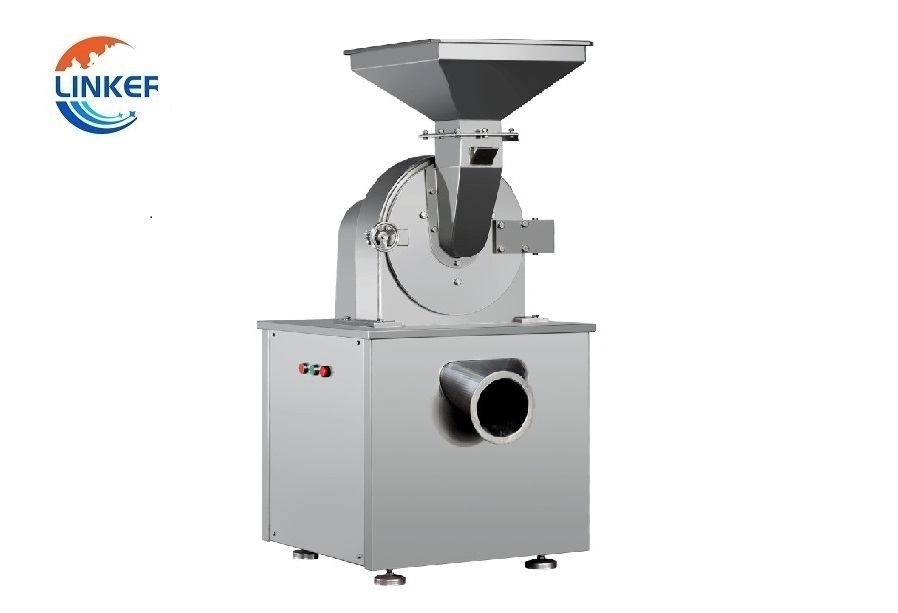
WF Universal Grinder – Hammer Mill
- Feeding Granularity: 10~15mm;
- Powder Size: 20-150mesh
- Capacity: 60-2000kg/h
- Motor Power (KW): 4-30kw;
- Axis Rotating Speed(r/min):2200~5300;
- Dimension(mm):500*500*1200~1800*1200*2500.
- FOB Unit Price: 1 unit $ 2,862~17,538. More than 5 units: $2,585~1,5785 Video
- Application: metal, Medicine, potato, bean, rice, herb, pepper, grain, food, corn, Sugar
Universal Meat Grinder
A universal meat grinder is a kitchen tool designed for grinding various types of meat. It typically consists of a hand-cranked grinder with a series of blades and plates that can be adjusted to achieve different levels of coarseness in the ground meat. The universal meat grinder can be used for a wide range of meat, including beef, pork, chicken, and even fish. Some models also come with attachments for making sausages or other types of ground meat products. A universal meat grinder is a great tool for home cooks who want to control the quality and freshness of their meat products and can be a valuable addition to any kitchen.
Universal Coffee Grinder:
The Universal Coffee Grinder is a versatile and high-quality grinder that can grind coffee beans to different levels of coarseness, making it suitable for a wide variety of coffee brewing methods. It is a manual hand-crank grinder that uses ceramic burrs to ensure a consistent grind size and preserve the coffee’s flavor and aroma.
The Universal Coffee Grinder is adjustable, allowing you to easily switch between grind sizes depending on your brewing method, from fine for espresso to coarse for French press. It is also easy to clean and maintain, making it a great choice for coffee lovers who want a reliable and long-lasting grinder.
Overall, the Universal Coffee Grinder is a great investment for any coffee enthusiast who wants to enjoy freshly ground coffee at home, with the flexibility to adjust their grind size to suit their preferred brewing method.
Universal Food Grinder:
The Universal Food Grinder is a versatile kitchen tool that can grind and mince a variety of foods, including meat, vegetables, nuts, and fruits. It is a manual hand-crank grinder that is easy to use and clean, with a sturdy construction that ensures long-lasting durability.
The Universal Food Grinder comes with different sized grinding plates, allowing you to choose the coarseness of your grind and achieve the desired texture for your dishes. It is also easy to disassemble, making it easy to clean and maintain.
Overall, the Universal Food Grinder is a great addition to any kitchen, providing a quick and easy way to grind and mince food for a variety of dishes, from meatballs and burgers to salsa and dips.
I. Introduction
Definition of a universal grinder
A universal grinder is a type of grinding machine that is capable of grinding various types of materials, such as metal, wood, plastics, and ceramics. It is called “universal” because it can perform multiple functions, including cylindrical, surface, and internal grinding, as well as taper grinding and thread grinding. The machine is designed to handle different workpiece sizes and shapes, making it a versatile tool in various industries, including automotive, aerospace, medical, and food processing.
II. Background
History and development of grinding machines
Grinding machines have a long and rich history dating back to the ancient times, where primitive stones were used for sharpening tools and weapons. Over time, various materials such as diamonds, emery, and carborundum were used for grinding.
The first grinding machine was invented in the 18th century by Englishman Henry Maudslay. This machine was used to manufacture precision parts for machines such as clocks and watches. In the 19th century, the development of steam power and the introduction of new materials such as cast iron led to the creation of more powerful and efficient grinding machines.
In the 20th century, grinding machines became more automated and specialized. The introduction of electric motors and hydraulics allowed for faster and more precise grinding operations. The development of high-speed steel and other advanced materials also contributed to the advancement of grinding machines.
Today, grinding machines are widely used in various industries such as automotive, aerospace, medical, and electronics. Modern machines are highly automated and can perform multiple operations, such as grinding, drilling, and milling, with high precision and accuracy. Advances in technology, including computer numerical control (CNC) and robotics, have also greatly improved the efficiency and quality of grinding operations.
Types of grinding machines
There are several types of grinding machines, each designed for a specific purpose. Here are some of the most common types:
- Surface grinder – A surface grinder is used to produce a smooth finish on flat surfaces. It uses a spinning wheel with abrasive particles to remove small amounts of material from the surface of a workpiece.
- Cylindrical grinder – A cylindrical grinder is used to grind the outside diameter of cylindrical workpieces. It can also be used to grind the inside diameter, creating a smooth, precise finish.
- Centerless grinder – A centerless grinder is used to grind cylindrical workpieces without the use of centers. The workpiece is supported by a work rest blade and rotated by a regulating wheel, while a grinding wheel removes material from the workpiece.
- Internal grinder – An internal grinder is used to grind the internal diameter of a workpiece. It uses a small grinding wheel mounted on a spindle to remove material from the inside of the workpiece.
- Tool and cutter grinder – A tool and cutter grinder is used to sharpen and recondition cutting tools, such as milling cutters and drill bits. It can also be used to produce custom tools.
- Jig grinder – A jig grinder is used to grind holes and shapes in jigs, fixtures, and dies. It uses a high-speed spindle and grinding wheels to produce precise, repeatable results.
- Gear grinder – A gear grinder is used to grind the teeth of gears for a smooth, precise finish. It can be used to produce gears of various sizes and shapes.
- Belt grinder – A belt grinder is a versatile machine used for grinding and polishing large, flat surfaces, as well as shaping and finishing metal and woodwork pieces.
There are many other types of grinding machines, including surface grinders with rotary tables, double-disc grinders, and thread grinders. The type of machine used depends on the type of material being ground, the precision required, and the production volume.
Uses of grinding machines in various industries
Grinding machines have a wide range of applications in various industries, including:
- Automotive industry – Grinding machines are used to produce precision parts for engines, transmissions, and other components. They are also used for surface finishing and polishing.
- Aerospace industry – Grinding machines are used to produce precision parts for aircraft engines, landing gear, and other components. They are also used for surface finishing and polishing.
- Medical industry – Grinding machines are used to produce precision parts for medical devices, such as implants and surgical instruments. They are also used for surface finishing and polishing.
- Food processing industry – Grinding machines are used to grind and process food products, such as coffee, grains, and spices. They are also used to produce food packaging materials.
- Electronics industry – Grinding machines are used to produce precision components for electronic devices, such as microchips and circuit boards. They are also used for surface finishing and polishing.
- Tool and die industry – Grinding machines are used to produce precision components for tool and die making, such as cutting tools and molds.
- Mining industry – Grinding machines are used to grind and crush minerals and ores for further processing.
- Construction industry – Grinding machines are used for surface preparation of concrete floors, as well as for the grinding and polishing of natural stone.
Overall, grinding machines are essential tools for manufacturing and fabrication in many different industries. They provide precise, efficient, and repeatable grinding operations, resulting in high-quality parts and products.
III. Design and Components of a Universal Grinder
The design and components of a Universal Grinder
A universal grinder is a versatile grinding machine that is capable of performing multiple functions, such as cylindrical, surface, internal, and taper grinding, as well as thread grinding. Here are the main design and components of a universal grinder:
- Bed – The bed is the main structure of the universal grinder and provides a stable base for the other components. It is typically made of cast iron and provides a rigid and stable platform for the workpiece.
- Headstock – The headstock holds the workpiece and rotates it during grinding operations. It is usually driven by an electric motor and can be adjusted to accommodate different workpiece sizes and shapes.
- Tailstock – The tailstock supports the other end of the workpiece and can be moved along the bed to adjust the length of the workpiece. It can also be used to hold a center for cylindrical grinding operations.
- Grinding wheel – The grinding wheel is the main tool used for grinding operations. It is mounted on a spindle and rotates at high speed to remove material from the workpiece. Different types of grinding wheels can be used for different types of grinding operations.
- Wheelhead – The wheelhead houses the grinding wheel and can be moved along the bed to adjust the depth of cut. It can also be swiveled to grind tapered surfaces.
- Workhead – The workhead can be swiveled to grind angled surfaces and can be adjusted to hold different types of workpieces. It may also be equipped with a center for cylindrical grinding operations.
- Control panel – The control panel houses the controls and displays for the machine. It allows the operator to set various parameters, such as wheel speed, feed rate, and depth of cut.
- Coolant system – A coolant system is used to cool and lubricate the grinding wheel and workpiece, preventing overheating and reducing friction. It also helps to remove swarf and other debris from the grinding area.
Overall, the design and components of a universal grinder are optimized for precision, versatility, and efficiency. The machine can perform a wide range of grinding operations with high accuracy and repeatability, making it a valuable tool in various industries.
Working principle of Universal Grinder
The working principle of a universal grinder is based on the principle of abrasion, where the grinding wheel removes material from the workpiece by friction and cutting. Here are the steps involved in the working principle of a universal grinder:
- Setup – The workpiece is securely mounted between the headstock and tailstock of the universal grinder, and the grinding wheel is positioned close to the workpiece.
- Grinding – The grinding wheel rotates at high speed and is fed into the workpiece by the wheelhead. The grinding wheel removes material from the workpiece by friction and cutting, resulting in a precisely shaped and finished surface.
- Cooling and lubrication – During the grinding process, a coolant is used to cool and lubricate the grinding wheel and workpiece, preventing overheating and reducing friction. The coolant also helps to remove swarf and other debris from the grinding area.
- Finishing – After the grinding operation is complete, the workpiece is checked for accuracy and surface finish. If necessary, the workpiece can be further finished by polishing or other surface treatments.
The universal grinder can perform a wide range of grinding operations, including cylindrical, surface, internal, and taper grinding, as well as thread grinding. The machine is highly versatile and can be used for both small and large-scale production runs. The precision and repeatability of the universal grinder make it a valuable tool in various industries where precision grinding is required.
IV. Advantages of Universal Grinder
Efficiency in Universal Grinder grinding operations
Efficiency in universal grinder grinding operations can be achieved through several methods, including:
- Proper machine setup – The machine must be properly set up before starting any grinding operation. This includes ensuring the workpiece is securely mounted, the grinding wheel is properly aligned, and the coolant system is functioning correctly. Proper setup will ensure that the grinding operation is performed accurately and efficiently.
- Proper selection of grinding wheel – The selection of the correct grinding wheel is critical for achieving efficiency in grinding operations. The correct wheel must be chosen based on the type of material being ground, the type of grinding operation being performed, and the desired surface finish. Using the correct wheel will result in faster grinding times, better surface finishes, and longer wheel life.
- Control of grinding parameters – The control of grinding parameters, such as wheel speed, feed rate, and depth of cut, can significantly impact grinding efficiency. These parameters should be carefully monitored and adjusted as needed to achieve the desired grinding results.
- Automation – The use of automation technology, such as computer numerical control (CNC), can greatly improve grinding efficiency. CNC technology allows for precise control of grinding parameters, reduces setup times, and enables the machine to perform complex grinding operations with high accuracy and repeatability.
- Continuous improvement – Continuously improving the grinding process through optimization and innovation can lead to increased efficiency. This can be achieved through the use of new technologies, such as advanced grinding wheel materials and coatings, or through process improvements, such as improved coolant delivery systems or new machine designs.
Overall, achieving efficiency in universal grinder grinding operations requires proper machine setup, proper selection of grinding wheels, control of grinding parameters, the use of automation technology, and continuous improvement. By implementing these methods, manufacturers can reduce grinding times, increase productivity, and improve the quality of their products.
Versatility in handling different types of materials
Universal grinders are highly versatile machines that can handle a wide range of materials, including metals, plastics, ceramics, and composites. The machine’s versatility is due to the ability to use different types of grinding wheels, each designed for a specific material and grinding operation. Here are some examples of materials that can be ground using a universal grinder:
- Metals – Universal grinders can grind a wide range of metals, including steel, stainless steel, aluminum, brass, and copper. The machine can be used for both rough and finish grinding operations, depending on the desired surface finish.
- Plastics – Universal grinders can also be used to grind plastic materials, including thermoplastics and thermosets. The machine can be used to grind plastics to a specific size and shape, or to remove excess material from plastic parts.
- Ceramics – Universal grinders are also capable of grinding ceramic materials, including alumina, zirconia, and silicon carbide. The machine can be used for both surface and internal grinding of ceramic parts.
- Composites – Universal grinders can also be used to grind composite materials, such as carbon fiber and fiberglass. The machine can be used to remove excess material from composite parts, or to shape them to a specific size and shape.
The versatility of universal grinders makes them a valuable tool in various industries, including aerospace, automotive, medical, and electronics. The ability to handle a wide range of materials and grinding operations allows manufacturers to produce high-quality parts with precision and accuracy.
High precision and accuracy in Universal Grinder grinding
Universal grinders are capable of achieving high levels of precision and accuracy in grinding operations. The following are some factors that contribute to the machine’s high precision and accuracy:
- Rigidity – Universal grinders are designed to be rigid and stable, minimizing the effects of vibration and thermal expansion. This rigidity ensures that the machine maintains its accuracy during the grinding operation.
- Precision bearings – Universal grinders use high-precision bearings to ensure that the grinding wheel and workpiece rotate smoothly and accurately.
- CNC technology – Many modern universal grinders are equipped with computer numerical control (CNC) technology. CNC technology allows for precise control of grinding parameters, such as wheel speed and feed rate, ensuring that the grinding operation is performed with high accuracy and repeatability.
- Advanced grinding wheel technology – Universal grinders can be equipped with advanced grinding wheel technology, such as vitrified or resin-bonded grinding wheels. These grinding wheels are designed to deliver high levels of precision and accuracy in grinding operations.
- Metrology equipment – Universal grinders can be equipped with metrology equipment, such as touch probes or laser measurement systems. These systems allow for real-time measurement and feedback during the grinding operation, ensuring that the part is being ground to the correct specifications.
The high precision and accuracy of universal grinders make them suitable for various applications where tight tolerances are required, such as aerospace and medical industries. Additionally, the ability to perform multiple grinding operations in a single setup reduces the need for multiple machines, saving time and increasing efficiency.
V. Applications of Universal Grinder
Industrial applications of Universal Grinder
Universal grinders have a wide range of industrial applications, including:
- Aerospace industry – Universal grinders are used in the aerospace industry to grind precision components such as turbine blades, shafts, and landing gear components. The high precision and accuracy of universal grinders make them ideal for producing parts with tight tolerances required in the aerospace industry.
- Automotive industry – Universal grinders are used in the automotive industry to produce precision components such as engine components, transmission gears, and brake rotors. The ability of universal grinders to perform multiple grinding operations in a single setup makes them efficient and cost-effective.
- Medical industry – Universal grinders are used in the medical industry to produce precision components such as surgical instruments, dental implants, and prosthetics. The high precision and accuracy of universal grinders are crucial in producing parts that meet the strict tolerances and surface finish requirements of the medical industry.
- Electronics industry – Universal grinders are used in the electronics industry to produce precision components such as circuit board components and connectors. The ability to perform multiple grinding operations in a single setup makes them an efficient and cost-effective option for producing high-quality electronic components.
- Tool and die industry – Universal grinders are used in the tool and die industry to produce precision cutting tools, dies, and molds. The high precision and accuracy of universal grinders make them ideal for producing complex shapes and geometries required in the tool and die industry.
Overall, the versatility, precision, and accuracy of universal grinders make them suitable for a wide range of industrial applications, where high-quality precision components are required.
Medical and dental applications of Universal Grinder
Universal grinders have a range of applications in the medical and dental industries, where precision and accuracy are crucial for producing high-quality parts. Here are some examples of medical and dental applications of universal grinders:
- Surgical instruments – Universal grinders are used to grind surgical instruments such as scalpels, forceps, and retractors. The high precision and accuracy of the machine ensure that the instruments are ground to the exact specifications required for their specific applications.
- Dental implants – Universal grinders are used to produce precision components for dental implants such as abutments, bridges, and crowns. The ability to perform multiple grinding operations in a single setup ensures that the components are produced efficiently and accurately.
- Prosthetics – Universal grinders are used to produce precision components for prosthetic devices such as hip implants, knee implants, and spinal implants. The high precision and accuracy of the machine are essential for ensuring that the components fit correctly and function properly.
- Bone cutting and shaping – Universal grinders are used to cut and shape bone in orthopedic surgeries. The machine can be used to precisely shape bone to fit implants or to remove damaged bone.
- Endodontic files – Universal grinders are used to produce precision endodontic files for root canal treatments. The machine can produce files with a specific shape and size required for the particular root canal treatment.
In the medical and dental industries, the high precision and accuracy of universal grinders are crucial for producing parts that meet the strict tolerances and surface finish requirements. Additionally, the ability to perform multiple grinding operations in a single setup makes universal grinders an efficient and cost-effective option for producing high-quality medical and dental components.
Food processing applications of Universal Grinder
Universal grinders also have applications in the food processing industry, where they are used to grind a variety of food products. Here are some examples of food processing applications of universal grinders:
- Meat grinding – Universal grinders are used to grind meat for the production of sausages, hamburgers, and other meat-based products. The machine can grind meat into different textures and sizes, depending on the specific application.
- Nut grinding – Universal grinders are used to grind nuts such as almonds, peanuts, and cashews into a fine powder or paste. The machine can produce nut butters, which are used in a variety of food products such as spreads, candies, and baked goods.
- Spice grinding – Universal grinders are used to grind spices such as black pepper, cumin, and coriander. The machine can grind the spices into a fine powder, which is used in a variety of food products such as curries, soups, and sauces.
- Grain milling – Universal grinders are used to mill grains such as wheat, rice, and corn. The machine can produce different textures of flour, depending on the specific application.
- Coffee grinding – Universal grinders are used to grind coffee beans into a fine powder or a coarse grind, depending on the specific brewing method. The machine can produce consistent particle size, which is important for producing high-quality coffee.
In the food processing industry, the high precision and accuracy of universal grinders are important for producing consistent particle size, which is crucial for the quality and texture of the final product. Additionally, the machine’s ability to perform multiple grinding operations in a single setup makes it efficient and cost-effective for food processing applications.
VI. Future Developments and Innovations
Current research and development in universal grinders
There are ongoing research and development efforts to improve the performance, efficiency, and capabilities of universal grinders. Some areas of current research and development in universal grinders include:
- Advanced control systems – The use of advanced control systems, such as artificial intelligence and machine learning, can optimize the grinding process and improve accuracy and precision.
- New materials and coatings – The development of new materials and coatings for grinding wheels can increase their durability, reduce wear, and improve grinding performance.
- Automation and robotics – The integration of automation and robotics into the grinding process can improve efficiency, reduce labor costs, and improve safety by reducing the need for manual operation.
- Energy efficiency – Energy efficiency is becoming an important consideration in the design of universal grinders. Research is being done to develop more energy-efficient motors, drives, and controls to reduce energy consumption.
- Additive manufacturing – Additive manufacturing techniques, such as 3D printing, are being explored for the production of grinding wheels with complex geometries and tailored properties.
- Smart sensors – The use of smart sensors can provide real-time monitoring of the grinding process, allowing for adjustments to be made to optimize performance and prevent damage.
These research and development efforts are expected to lead to the development of more advanced and efficient universal grinders with improved performance, precision, and capabilities.
Future innovations and improvements of universal grinders
There are several potential future innovations and improvements in the field of universal grinders, including:
- Integration with Industry 4.0 technologies – Universal grinders could be integrated with Industry 4.0 technologies such as the Internet of Things (IoT), big data analytics, and cloud computing. This could enable real-time monitoring of grinding parameters, remote control and diagnosis, and predictive maintenance.
- Advanced abrasive materials – Advanced abrasive materials such as diamond composites, CBN (cubic boron nitride), and nanocrystalline diamond coatings could be used to improve the durability, efficiency, and precision of grinding wheels.
- Modular design – A modular design approach could enable the customization and reconfiguration of universal grinders for different applications and workpieces.
- Improved automation and robotics – Advances in automation and robotics could enable universal grinders to operate autonomously, reduce operator intervention, and improve safety and productivity.
- High-performance computing – The use of high-performance computing (HPC) could enable complex simulations and modeling of the grinding process, leading to improved understanding and optimization of the process.
- Sustainability and energy efficiency – Future universal grinders could be designed to be more sustainable and energy-efficient, reducing their environmental impact and operating costs.
Overall, future innovations and improvements in universal grinders are expected to increase their efficiency, precision, and versatility, and enable new applications in a range of industries.
Business Type: | Manufacturer/Factory | Main Products: | Mill, grinder, granulator, mixer, Crushing Equipment |
Number of Employees: | 100 | Year of Establishment: | 2014.05 |
Production Capacity | 5000Set/Year | After-sales Service: | Technical Support; on-line teach lessons |
R&D Capacity: | ODM, OEM | Annual Output Value: | US$5 Million – US$10 Million |
No. of R&D Staff: | 5 | No. of Production Lines: | 6 |
LK Mixer is a professional manufacturer for grinder, mixer and pulverizer. These machines are widely used in pharmaceutical, cosmetic, health care products and chemical industries. Our main product including granulating machine, grinder, mixer, dryer, etc. All mechanical products in accordance with the China GMP design requirements. And also we have other certifications such as CE, UL for motors.
Business Philosophy
“Quality is the main policy of sales” and “integrity is the principle of success” are the business philosophy of our people. We carry out one-year warranty, lifelong maintenance service, with technical consultation, with material test machine and other services, and long-term supply of equipment. Welcome new and old customers to negotiate cooperation!
Certifications:
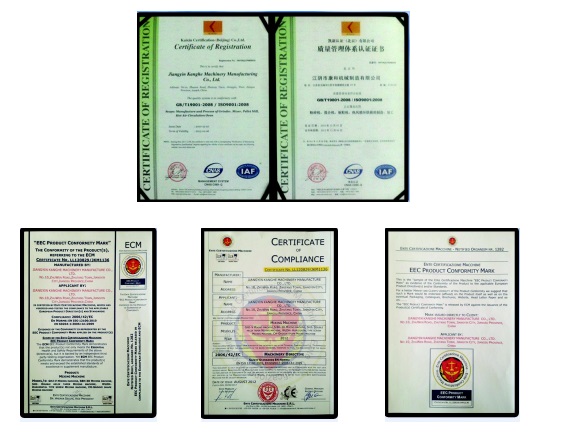
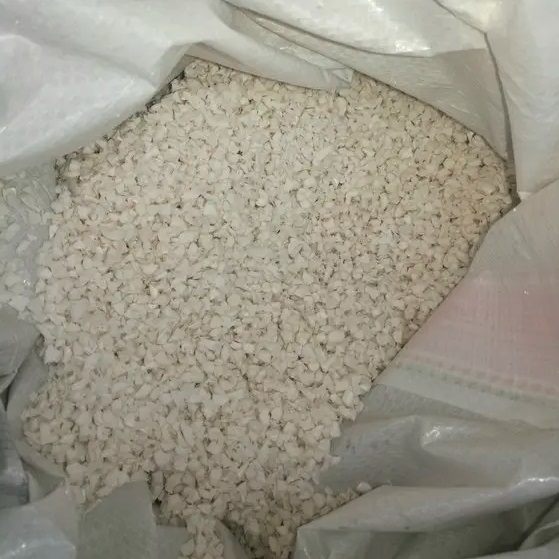
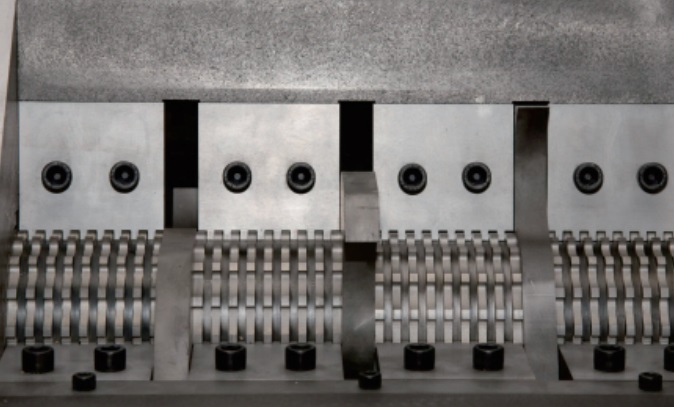
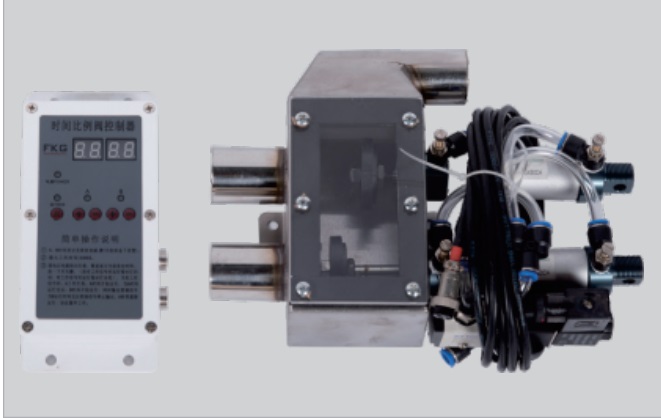
Electric Cabinet with UL Certification
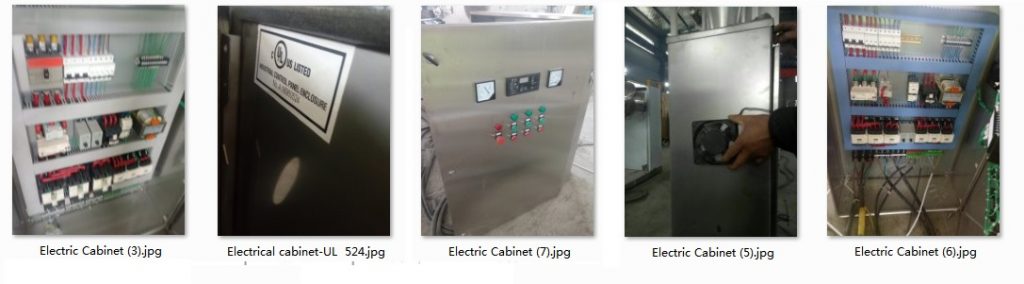
Cyclone Processor and Motors:
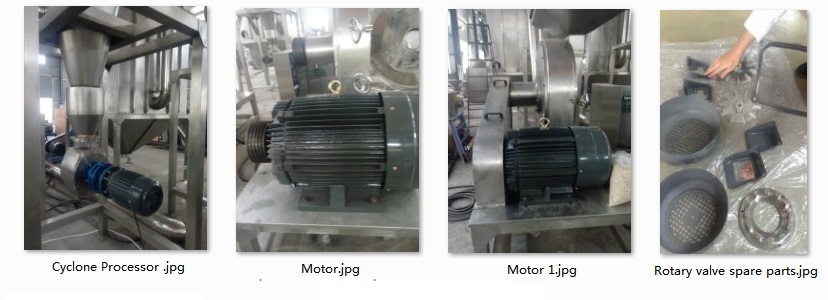
Spare Parts:
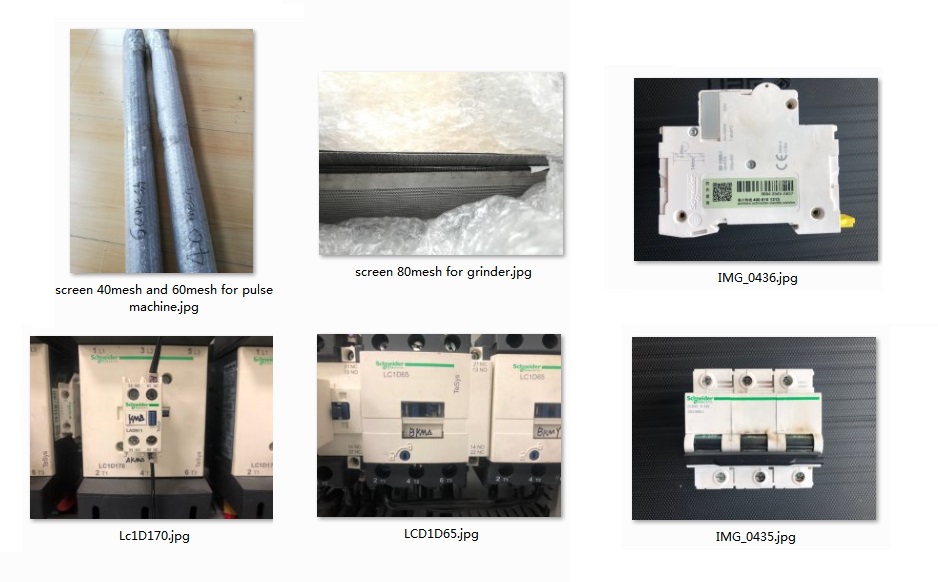
Small Machine Packing:
Small machine packed with export fumigation-free wooden cases, goes with bulk shipment or in container.
When packing small machines for sea shipment, it is important to take measures to ensure that the machines are protected from damage during transit. Here are some general steps that a manufacturer may follow when packing small machines for sea shipment:
- Clean and dry the machine: Before packing, the machine should be thoroughly cleaned and dried to prevent any moisture or debris from causing damage during transit.
- Disassemble the machine: If possible, the machine should be disassembled into its component parts to reduce its overall size and make it easier to pack.
- Wrap the machine in protective material: The machine should be wrapped in a layer of protective material, such as bubble wrap or foam, to protect it from scratches and impact during transit.
- Place the machine in a sturdy box: The wrapped machine should then be placed in a sturdy box that is appropriate for the size and weight of the machine. The box should be made of durable material, such as corrugated cardboard or plywood, and should be able to withstand the rigors of sea transit.
- Add packing material: The box should be filled with packing material, such as packing peanuts or air pillows, to provide cushioning and prevent the machine from shifting during transit.
- Seal the box: The box should be securely sealed with high-quality packing tape to prevent it from opening during transit.
- Label the box: The box should be clearly labeled with the machine’s name, weight, and any other relevant information, as well as the destination address and contact information.
Overall, the goal is to pack the small machine in a way that will protect it from damage during transit and ensure that it arrives at its destination in good condition. It is important to follow proper packing procedures and use high-quality packing materials to minimize the risk of damage during sea shipment.
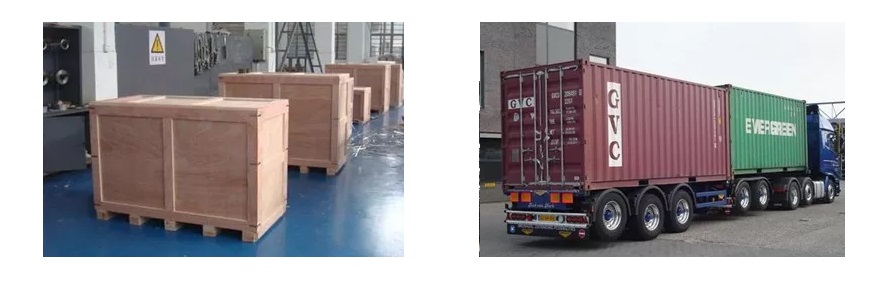
Large Machine Packing:
Packing a large machine for sea shipment can be a complex and challenging task. However, with careful planning and attention to detail, it is possible to pack a large machine for sea shipment in a way that will ensure that it arrives at its destination in good condition. Here are some general steps that a manufacturer may follow when packing up a large machine for sea shipment:
- Clean and prepare the machine: Before packing, the machine should be thoroughly cleaned and prepared. All fluids, such as oil or coolant, should be drained, and any loose or detachable parts should be removed.
- Disassemble the machine: If possible, the machine should be disassembled into its component parts to reduce its overall size and make it easier to pack. Each part should be carefully labeled and numbered to ensure that it can be easily reassembled at the destination.
- Protect delicate parts: Delicate or fragile parts should be wrapped in protective material, such as bubble wrap or foam, to protect them from damage during transit.
- Build a custom crate: A custom crate should be built around the machine to provide a secure and sturdy enclosure. The crate should be made of durable material, such as plywood, and should be designed to fit the machine snugly. The crate should also include braces or supports to prevent the machine from shifting during transit.
- Add cushioning material: The crate should be filled with cushioning material, such as packing peanuts or air pillows, to provide extra protection and prevent the machine from moving or shifting during transit.
- Securely fasten the machine: The machine should be securely fastened to the crate to prevent it from moving or shifting during transit. This may involve using straps, bolts, or other fasteners to hold the machine in place.
- Seal and label the crate: The crate should be securely sealed with high-quality packing tape, and should be clearly labeled with the machine’s name, weight, and any other relevant information. The destination address and contact information should also be clearly marked on the crate.
Overall, packing a large machine for sea shipment requires careful planning and attention to detail. It is important to use high-quality materials and follow proper packing procedures to ensure that the machine arrives at its destination in good condition. A professional packing and shipping company may be consulted to ensure that the machine is properly packed and prepared for sea shipment.
Customer Side Machine Groups Showcase Videos:
Dust Collector Shipment
Shipment – Packing Method
Two Large Industrial Grinder Ready to Ship
Domestic Shipment Show Case:
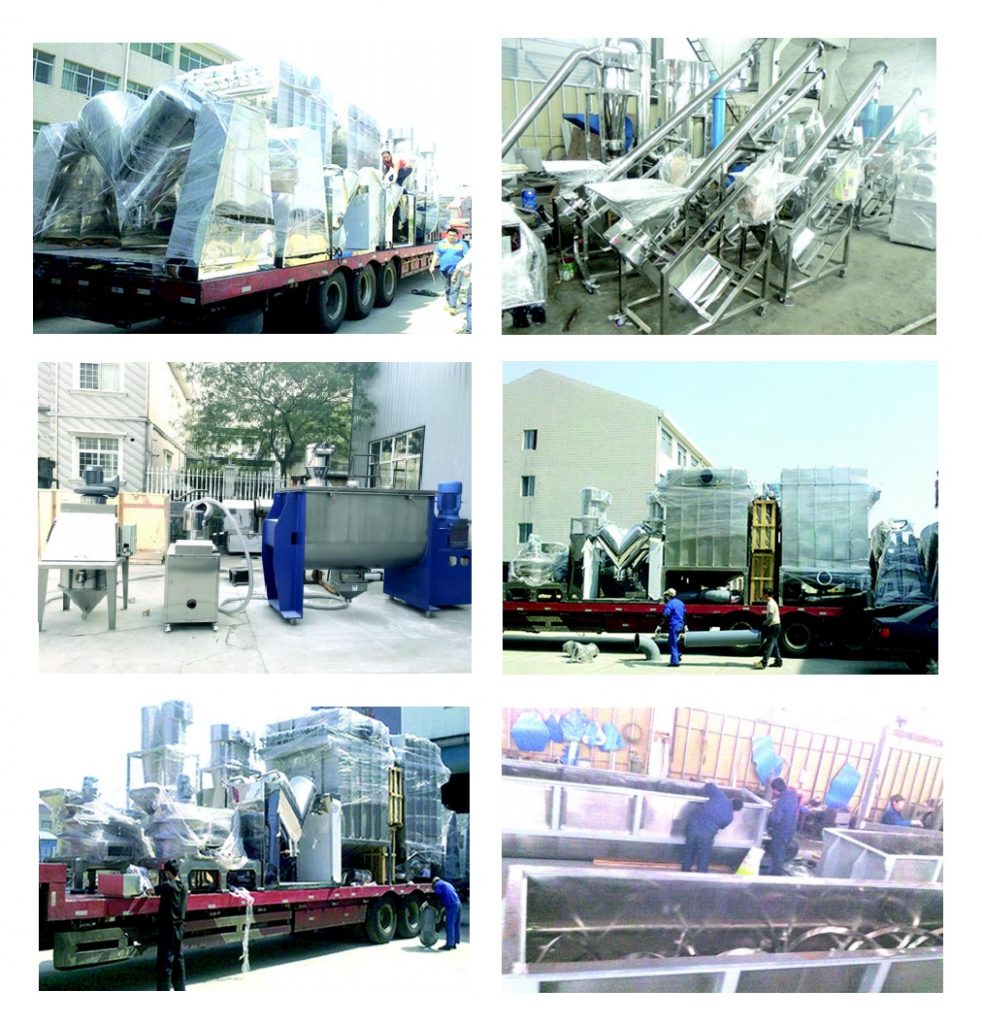
Installation Layout:
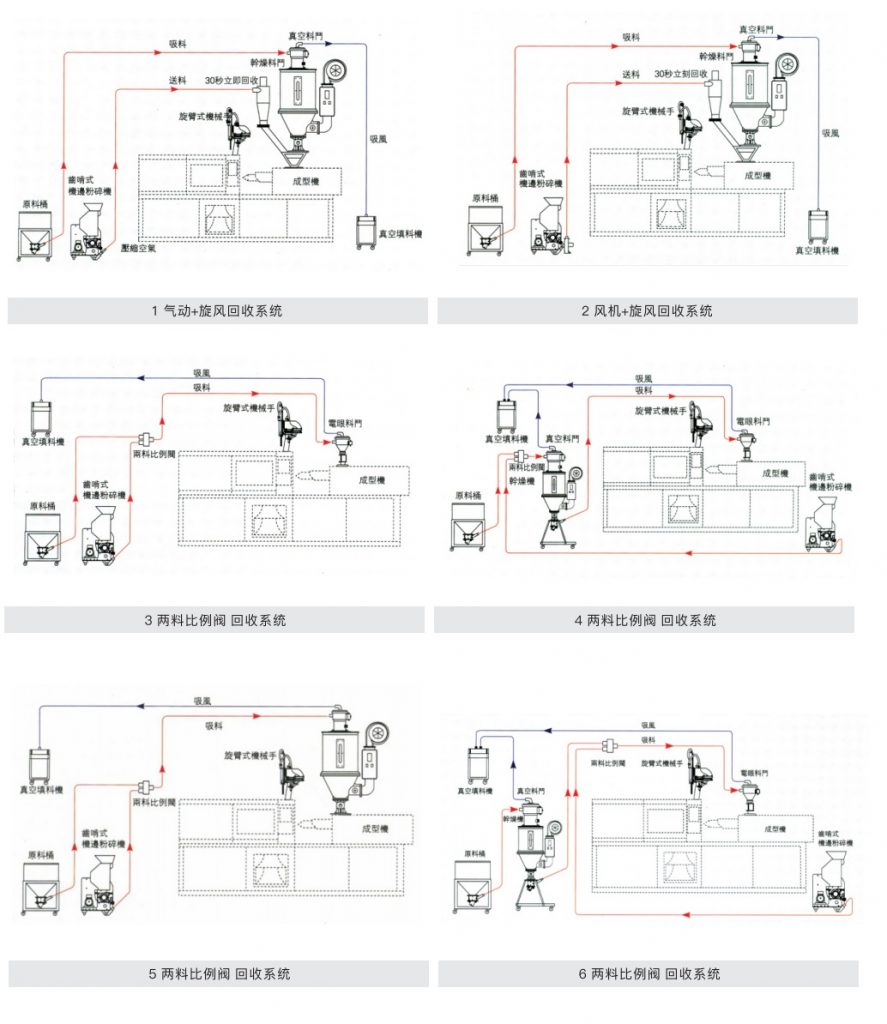
Maintenance and Safety Measures
Proper maintenance practices for the machine
Proper maintenance practices are essential for ensuring the efficient and safe operation of a universal grinder. Here are some maintenance practices that should be followed:
- Regular cleaning – The machine should be cleaned regularly to remove any debris, dust, or coolant that may accumulate on the machine’s surfaces. This can be done using a soft brush, air hose, or a cleaning solution.
- Lubrication – The machine’s moving parts should be lubricated regularly to reduce friction and wear. The manufacturer’s recommendations for lubrication intervals and types should be followed.
- Inspection – The machine should be inspected regularly for any signs of wear, damage, or misalignment. Any issues should be addressed immediately to prevent further damage or safety hazards.
- Replacement of worn or damaged parts – Worn or damaged parts should be replaced immediately with genuine parts from the manufacturer.
- Calibration – The machine should be calibrated regularly to ensure that it is operating within the specified tolerances and accuracy.
- Operator training – Proper operator training is essential for ensuring the safe and efficient operation of the machine. Operators should be trained on the proper operation, maintenance, and safety procedures for the machine.
- Record keeping – A maintenance log should be kept to track the machine’s maintenance history, including cleaning, lubrication, inspection, and repairs. This can help identify any trends or issues that need to be addressed.
Following these maintenance practices can help ensure the safe and efficient operation of a universal grinder, prolong its lifespan, and reduce the risk of downtime and costly repairs.
Safety measures for operators and workers
Safety measures for operators and workers are crucial when using a universal grinder. Here are some safety measures that should be followed:
- Personal protective equipment (PPE) – Operators and workers should wear appropriate PPE, including safety glasses, hearing protection, gloves, and safety shoes.
- Machine guards – The machine should be equipped with proper machine guards to prevent access to the grinding wheel during operation. The guards should be in good condition and properly installed.
- Lockout/tagout procedures – Lockout/tagout procedures should be followed to ensure that the machine is not accidentally started or energized during maintenance or repair.
- Training – Operators and workers should receive proper training on the safe operation of the machine, including the use of PPE, machine guards, and lockout/tagout procedures.
- Inspection – The machine should be inspected regularly for any signs of wear, damage, or misalignment that may pose a safety hazard.
- Proper use of grinding wheels – Operators should ensure that the grinding wheel is properly installed, dressed, and aligned. The grinding wheel should not be overloaded or forced into the material being ground.
- Proper handling of coolant – If coolant is used, operators should ensure that it is properly mixed, applied, and contained. Coolant should not be allowed to accumulate on the floor, as it can create a slipping hazard.
- Emergency procedures – Emergency procedures should be established and communicated to all operators and workers in case of an accident or injury.
Following these safety measures can help prevent accidents and injuries when using a universal grinder. It is important to prioritize safety and ensure that all operators and workers are trained and informed about the potential hazards of the machine.
About LKMixer
LKMixer is a professional manufacturer for fertilizer production line, grinder, mixer and granulator, shredder. These machines are widely used in food, pharmaceutical, cosmetic, health care products and chemical industries. The Food materials like Peanut, mushroom, seeds, potato, bean, tobacco, salt, cannabis, tea, Sugar, corn, Coffee, rice, pepper, grain as so on. Grinders have many types such as Pulse Dust Grinder which suitable for zero pollution environment, Turbine Mill which is suitable for coffee bean, 12-120mesh all can meet, Ultrafine Grinding Mill covers 80-200mesh, and also Winnowing Dust Grinder or other grinding machines like SF Hammer. Welcome to contact us for details. Contact us for more information. Proposal, catalog, quotation. Mobile/WhatsApp: +86 18019763531 Tel: +86 21 66037855 Email: sales@lkmixer.com
Contact Us
Universal Grinder Youtube Video (See More)
FAQ(Click and See More)
What is the difference between a cylindrical grinder and a universal grinder?
A cylindrical grinder and a universal grinder are both types of grinding machines, but there are some differences between them.
A cylindrical grinder is a machine tool that is used to shape the outside of an object. It has a wheel that rotates on a horizontal axis and the object is held in place between a center and a chuck. The object is rotated and the grinding wheel removes material from the outside surface of the object. Cylindrical grinders are typically used to create round shapes, such as cylinders or cones, and they are commonly used in manufacturing and metalworking industries.
A universal grinder, on the other hand, is a type of cylindrical grinder that can perform a variety of grinding operations. In addition to the cylindrical grinding capabilities of a standard cylindrical grinder, a universal grinder can also perform internal grinding, centerless grinding, and other types of grinding operations. This is achieved through the use of additional attachments and accessories that can be fitted to the machine.
In summary, while a cylindrical grinder is designed specifically for shaping the outside of an object, a universal grinder is designed to perform a wider range of grinding operations, including internal grinding and centerless grinding.